Tensile Testing Machine
The Tensile Testing Machine Biopdi aim to perform quickly, effectively and accurately most of the mechanical tests on materials and products. The Tensile Testing Machine can perform several types of mechanical tests such as: tensile test, compression test, shear test, bending test, flexural test, shear test and others. To find out more details about the Tensile Testing Machine, visit our article page.
Due to its versatility, the Tensile Testing Machine is used in several types of segments such as: metal-mechanics, civil construction, polymers, plastic, textile, wood, footwear, medical-dental, furniture, automotive, among others, meeting the most varied standards national and international as ISO, ASTM, DIN, ABNT NBR.
The Tensile Testing Machine is a common name given to the Universal Testing Machine, as the tensile test is the most used test in different areas, it is common to find these denomination, but it is the same equipment.
Tensile Testing Machine:
Discover our full portfolio
The Tensile Testing Machine with an electromechanical drive has a wide range of load capacities, ranging from 0,2 kN (200kgf) to 1 MN (100,000 kgf). To conduct the tests, it offers several models of grips, devices, and extensometers for a variety of mechanical tests. The Tensile Testing Machine also comes with software that allows for adjustments, configurations, data acquisition, analysis, and reporting of mechanical tests.
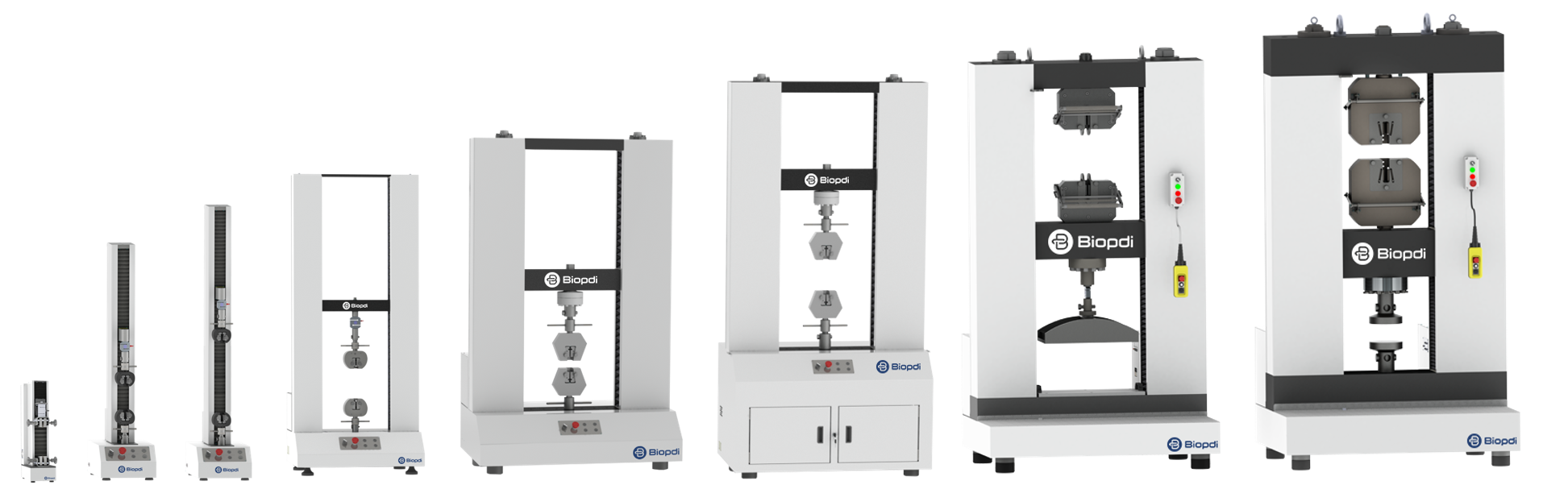
Biopdi has proprietary technology to develop, produce, and sell any type of tensile testing machine, allowing us to customize any parameter of the machine according to our customers’ needs. Please feel free to contact us if you require any equipment customization.
Tensile Testing Machine:
Models
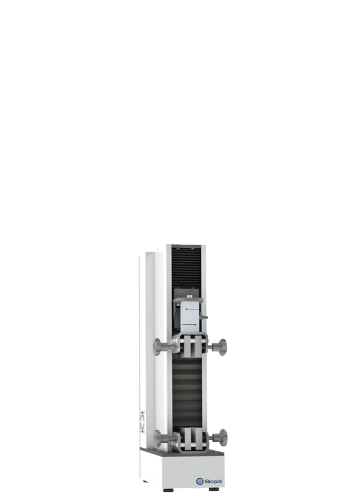
Portable:
200 N to 500 N
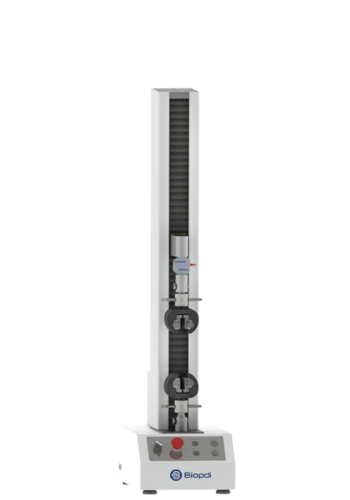
Single Column:
1 kN to 10 kN
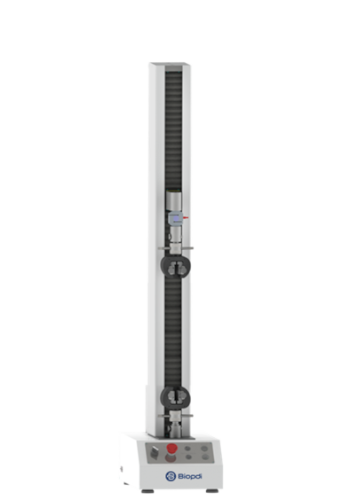
Single Colum Extended:
1 kN to 10 kN
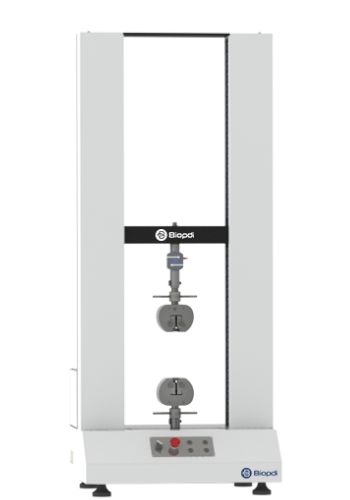
Dual Column:
5 kN to 50 kN
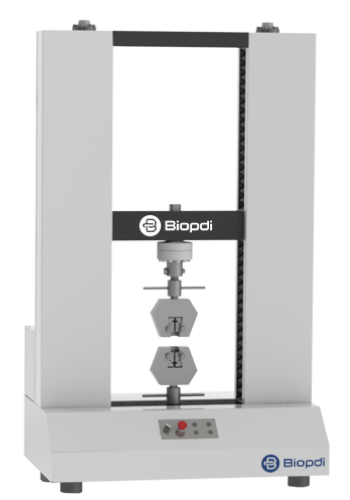
Dual Column:
100 kN to 150 kN
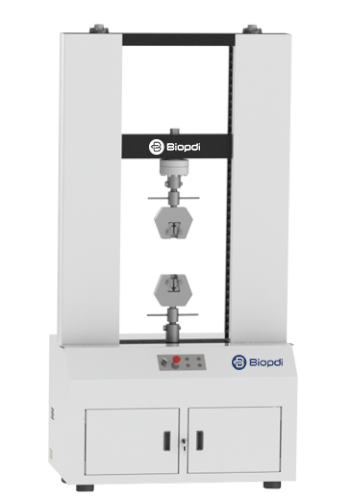
Self-supporting
100 kN to 150 kN
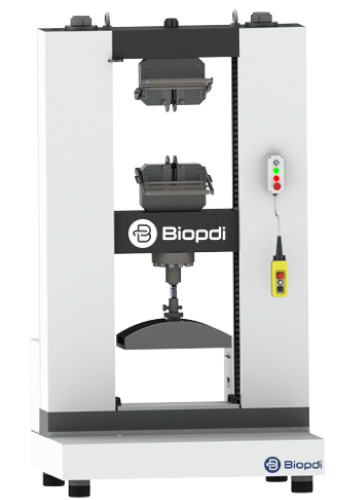
Self-supportting
200 kN to 300 kN
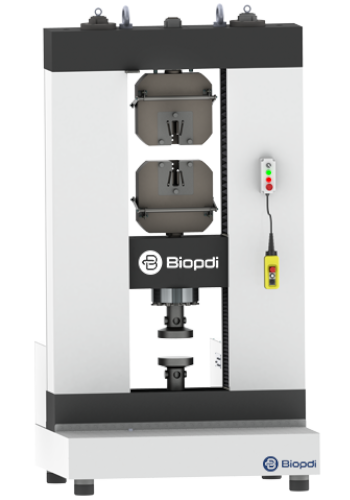
Self-supporting
600 kN to 1 MN (1000 kN)
Tensile Testing Machine:
Type of tests performed
TENSILE TEST
Tensile testing is a crucial mechanical test used to evaluate the strength and ductility of materials. It involves applying a controlled force. See more
COMPRESSION TEST
Compression testing is a fundamental evaluation method employed to assess a material’s ability to withstand compressive forces. See more
SHEAR TEST
Shear testing examines a material’s response to forces acting parallel to its surface. By applying a force that causes one part of the material. See more
BEND TEST
Bend testing is a mechanical test that determines a material’s flexibility and resistance to fracture under bending forces. See more
FLEXURAL TEST
Flexural testing, also known as the three-point bend test, is employed to measure a material’s resistance to bending or flexural stress. See more
FRICTION TEST
Coefficient of friction test measures the amount of resistance between two surfaces in contact when one moves relative to the other. See more
TEAR TEST
Tear test determines a material’s resistance to tearing forces, often encountered in applications involving thin films, fabrics. See more
PEEL TEST
Peel testing evaluates the strength of adhesion between two materials, typically an adhesive and a substrate. The test involves separating. See more
BOND TEST
Bond test measures the strength of a bond between two materials. It’s used in adhesive and weld test. It helps in determining the reliability of joints and interfaces. See more
INDENTATION TEST
Indentation Force Deflection (IFD) is used to characterize the cushioning or compressive properties of a material, especially foams and soft polymers. See more
FRACTURE TEST
Fracture toughness is a material’s ability to resist crack propagation. This property is vital for assessing a material’s suitability for applications where structural. See more
PUNCTURE TEST
Puncture test examines a material’s ability to withstand penetration by sharp objects or forces. This test to evaluate puncture strength and design materials. See more
CRUSH TEST
Crush resistance test measures a material’s ability to resist deformation, particularly in terms of compressive force. See more
TORSION TEST
Torsion testing is a critical method in materials engineering, examining how products and materials behave under twisting forces. See more
AXIAL TORSION TEST
Axial torsion test examines a material’s behavior when subjected to simultaneous axial and torsional loads. This test to study shear stress. See more
FATIGUE TEST
Fatigue Testing is the evaluation of a material’s endurance and failure under repeated stress and cyclic loading conditions. See more.
Tensile Testing Machine:
Main Features
- Single Column: Force Capacity – 500 N to 10 kN
- Double Column: Force Capacity – 5 kN to 1 MN (1000 kN)
- Minimum Test Speed = 0.0001 mm / min (Depending on model)
- Maximum Test Speed = 500 mm / min (Depending on model)
- Drive: through recirculating ballscrews loaded with cylindrical guide column system in relative to the spindles;
- Non volatile memory: calibration data of the transducers, such as load cells and strain gauges, stored in non-volatile memory, so that the independent calibration of the computer to which the machine is connected, data compilation and test control through software;
- Front panel – Mechanical with buttons (functions: on and off, up and down, home, reference and emergency)
Front panel – digital CLP (functions: on and off, up and down, speed setting, home, reference and emergency) (optional)
Touchscreen (optional) – has all the software’s parameters and settings, without the need to use a computer
- Measurement of interchangeable cell strength, class 1 accuracy (NM ISO 7500-1) or 0.5 (on request);
- Automatic recognition and adjustment of transducers, such as load cells and strain gauges;
- Displacement measurement using an optical sensor with a resolution of 0.0001mm (Depending on the model);
- Data communication: TCP-IP or USB or Serial;
- Displacement measurement channels and load included in the machine frame. It has the possibility of adding up to four strain channels to the machine frame, possibility of operation with the use of two channels that operation the same time and independently for LVDT strain (0 to 10 Vcc) and output extensometers;
- Software for making adjustments, configurations, acquisition, analysis and reporting of mechanical tests;
- Voltage: 100, 120, 220 or 240 VAC @ 47 to 63 Hz;
- Electrostatic external paint highly resistant to corrosion;
- International technical assistance;
- Instruction Manual;
- Easy cleaning and programming;
- One year guarantee for manufacturing defects;
- ISO 9001 Certification;
- Limit switch Mechanical manual and electronic limit switch (digital ruler) (optional)
Tensile Testing Machine:
Testing Acessories
In a tensile testing machine, grips and fixtures are crucial as they securely hold the test specimen in place while it’s subjected to tension. The nature of the material being tested, the geometry of the specimen, and the specific requirements of the test often determine the type of grip or fixture used. Here’s an overview of some common types of grips and fixtures and their uses:
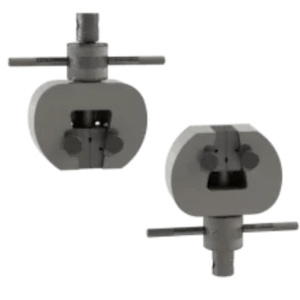
Wedge action grips
Wedge grip for tensile testing on materials used in the universal testing machine.
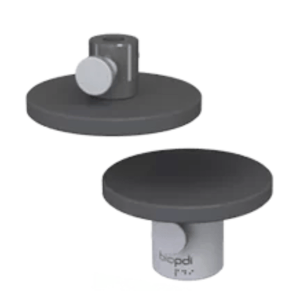
Compression test
Device used in material compression testing used in the universal testing machine.
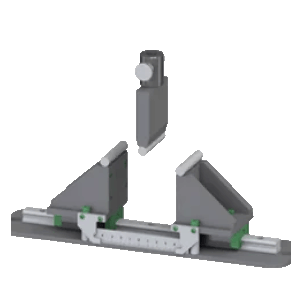
Bend test
Device used in bend and flexural testing (flexure testing) in the universal testing machine.
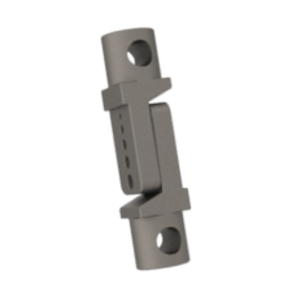
Shear test
Flat device for shear testing used in the universal testing machine.
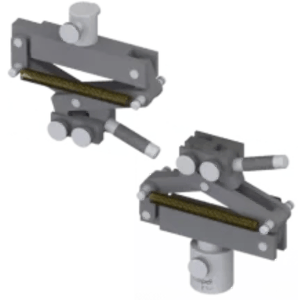
Tensile test – Lever grip
Lever grip: Material tensile test used in the universal testing machine.
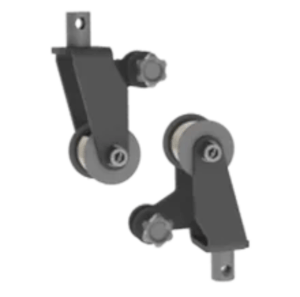
Wire tensile test
Roller device for wire test and materials used in the universal testing machine.
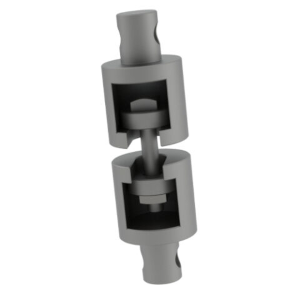
Nut tensile test
Device for tensile testing of bolt nuts with different dimensions.
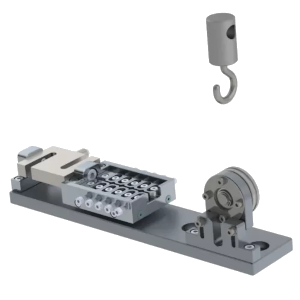
Orthodontic friction test
Tensile test device for determining the friction of orthodontic wires.
Other Testing Accessories
- Shear test;
- Compression test;
- Flexion test or bending test;
- Tensile testing;
- Tensile testing on springs and plastic seals;
- Dental resin tensile test;
- Bolt tensile test;
- Flexion test or bending test;
- Four point bending test;
- Bolt shear test;
- Tape adhesion test;
- Determination of the friction coefficient;
- Adhesion test;
- Microtensile Device;
- Electronic deflectometer
- Shear test on welded wire joints;
- Breaking test by embedding in plastic films;
- Steel sheet embedding test;
- Pullout test;
- Tear test;
- Drilling test;
Specialized Grips and Fixtures: Many grips and fixtures are designed for specific applications or specimen types. This includes vise grips for testing wires, thread grips for testing yarns, and many others.
Selecting the right grip or fixture is key to obtaining accurate and meaningful tensile test results. It should securely hold the specimen without causing it to prematurely fail at the gripping point, ensuring that the specimen fails within its gauge length.
Moreover, the grip or fixture must be compatible with the load cell capacity and the other testing conditions. Regular maintenance and inspection of grips and fixtures are also essential to ensure consistent performance and longevity.
Tensile Testing Machine:
Extensometers
An extensometer is a critical component of the tensile testing machine that is used to measure the elongation or strain of a specimen as it undergoes tensile stress. Strain is defined as the change in length of the material divided by the original length.
Accurate measurement of strain is crucial to the interpretation of tensile test results and the calculation of key material properties, such as the modulus of elasticity (Young’s modulus), yield strength, and elongation to fracture.
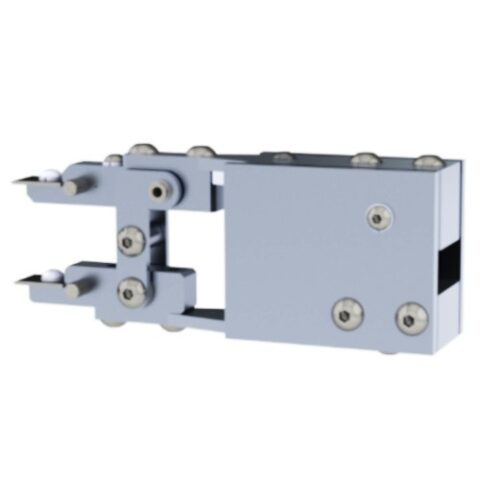
Extensometer of 25 mm
Extensometer used in small strain with an opening of 25 mm
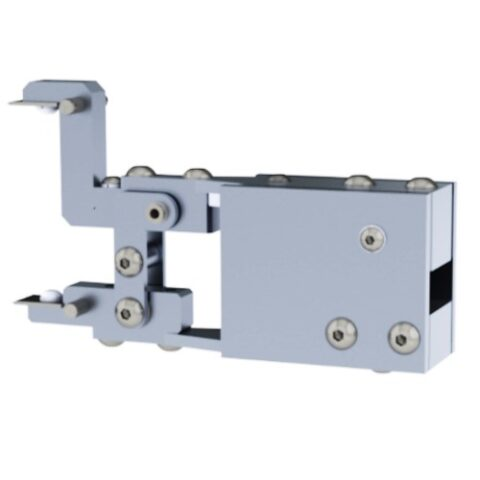
Extensometer of 50 mm
Extensometer used in small strain with an opening of 50 mm.
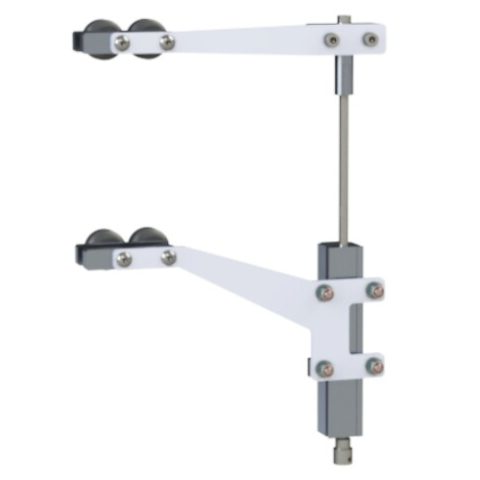
Extensometer of 150 mm
Extensometer used in medium strain (polymers) with an opening of 150 mm.
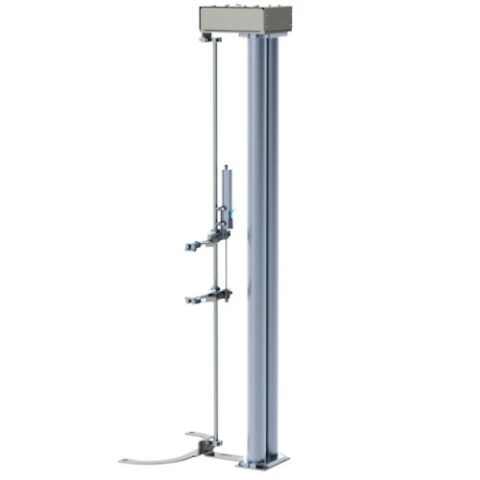
Extensometer of 250 mm
Extensometer used in medium strain (polymers) with an opening of 250 mm.
Here’s a more detailed look at the role of an extensometer in a tensile test:
- Initial Setup: An extensometer is typically attached to the specimen before the test begins. Depending on the type of extensometer, it can be attached at various points along the length of the specimen. It is essential that the extensometer is positioned correctly to ensure accurate measurements.
- Measurement During Test: As the tensile testing machine applies force to the specimen, causing it to stretch, the extensometer measures the change in length (or elongation) of the specimen. This data is sent to the machine’s control system in real-time.
- Data Analysis: The extensometer’s measurements are used to calculate strain, which is plotted against the applied stress to create a stress-strain curve. The slope of the initial linear portion of this curve gives the modulus of elasticity, and the point where the curve deviates from linearity gives the yield strength. The total elongation at the point of fracture can also be measured.
- Types of Extensometers: There are various types of extensometers, including clip-on extensometers, which physically attach to the specimen, and non-contact extensometers, which use optical or laser systems to measure deformation without touching the specimen. The choice of extensometer depends on the material being tested, the required accuracy, and the specific conditions of the test.
- Importance in Material Properties Evaluation: By providing an accurate measure of strain, extensometers enable the evaluation of material properties that are critical in determining a material’s suitability for various applications.
To ensure accurate results, it’s important to calibrate the extensometer regularly and to use it correctly according to the manufacturer’s instructions and the relevant testing standards.
Tensile Testing Machine:
Load Cells
In a tensile testing machine, load cells are used to measure the force exerted on the test specimen. Different load cells are capable of measuring different ranges of force, which is typically expressed in terms of capacity (for example, 50 N, 500 N, 5 kN, or even 1000 kN).
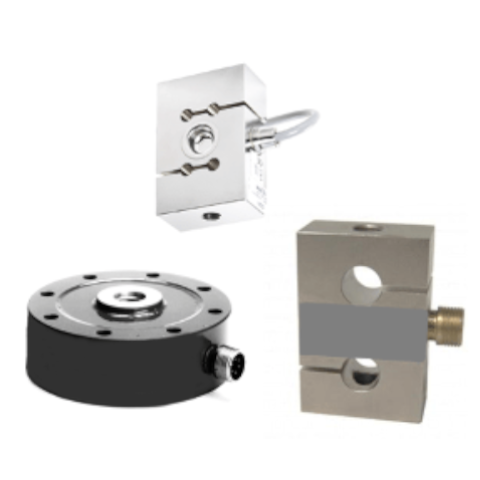
Capacity 10 N (1 kgf);
Capacity 100 N (10 kgf);
Capacity 500 N (50 kgf);
Capacity 1 kN (100 kgf);
Capacity 2 kN (200 kgf);
Capacity 5 kN (500 kgf);
Capacity 10 kN (1000 kgf);
Capacity 20 kN (2000 kgf);
Capacity 50 kN (5000 kgf);
Capacity 100 kN (10000 kgf);
Capacity 200 kN (20000 kgf);
Capacity 300 kN (30000 kgf);
Capacity 600 kN (60000 kgf);
Capacity 1000 kN (100000 kgf);
The specific range of a load cell is an important factor to consider when performing tensile/compression tests, as it must be appropriate for the force range expected during the test.
- Low Capacity Load Cells: Load cells with low capacities (e.g., 1 N to 500 N) are used for testing small or delicate specimens, or materials with low tensile strengths. They are ideal for precise measurements of small forces. Examples of their use could include testing thin plastic films, threads, or biomaterials.
- Medium Capacity Load Cells: Load cells with medium capacities (e.g., 1 kN to 50 kN) are often used for testing common engineering materials such as metals, polymers, and ceramics. They are used in applications where moderate levels of force are expected.
- High Capacity Load Cells: High capacity load cells (e.g., 100 kN to 1000 kN or more) are used for testing high-strength materials or large components. They are used in applications where high levels of force are expected, such as in the testing of steel, composite materials, or concrete specimens.
It’s essential to select a load cell with an appropriate capacity for the tensile/compression test being conducted. Using a load cell with too high a capacity can result in lower accuracy and resolution for small forces. Conversely, using a load cell with too low a capacity can risk overloading the load cell, which can cause inaccurate measurements or even damage the load cell.
Additionally, it’s important to note that most load cells provide their highest accuracy in the upper range of their capacity (usually above 10% of the maximum load). Thus, selecting a load cell that operates mostly in this range during a test can help ensure the most accurate and reliable results. Regular calibration and maintenance of load cells are also crucial to maintain their performance and longevity.
Tensile Testing Machine:
Main features of the software
The software used in the Universal Testing Machine has an interface between the operator and the machine, has functions for adjusting and configuring the test, analyzing and acquiring data for performing the tests of: Tensile test, compression test, shear test, bending test, among others. To connect to the machine in a computer with a Windows® 10 operating system is required, on which the software will be installed.
The Software has two versions:
Version Touchscreen: being used directly on the machine through a touchscreen (touch sensitive), without the need to use a computer, as it has a digital unit integrated into the structure of the machine.
Desktop Version: Can be installed on any desktop or notebook computer that communicates with the machine.
The main screens available in the universal testing machine software are shown below:
Below are descriptions of the main parameters and functions available in the universal testing machine software.
SETTINGS TAB
Status Monitor
Communication Port: In the “Communication Port” tab, a new COM port option will show for selection. Select the communication port that show.
Connection Status: Indicates whether the software is ready for use.
Lower limit switch: This is the lower maximum limit of the crossbar.
Upper limit switch: It is the maximum upper limit of the dash.
Load cell indicator: Indicates the capacity of the load cell when connected (green light), and indicates disconnected load cell (red light).
Emergency: Indicates whether the emergency button is activated.
Test types
Vertical positive: to tensile test.
Vertical Negative: for compression, shear, flexion/bending tests.
Test Speed: it is the speed at which the beam will perform the movement in the chosen test (positive vertical or negative vertical), this speed can be adjusted between 0.001mm / min and 500mm / min.
Manual adjustment
Up button: Triggers the upward movement of the crossbar.
Down Button: Triggers the downward movement of the crossbar.
Speed Indicator: Moves the crossbar up or downward with a controlled speed from 0.001 mm/ min to 500 mm/min.
Automatic Return
Home button: used to return to the referenced position, this reference is a specific point of the dash position determined by the operator on the machine panel.
Stop button: end the return triggered by the Home button.
Specimen section area
Section area of rectangle = (𝑎 × 𝑏) (depth x width).
Tube section area = (π × R2) – (π × r2) (Area of the largest circle minus the area of the smallest circle).
Cylinder section area = (𝜋 × 𝑅2) (Circle area).
Specimen length: Defines the length of the specimen.
Intersection line
When the flow phenomenon is not clearly observed, the yield stress corresponds to the necessary stress to promote a permanent deformation of 0.2% or another specified value (depending on the material);
Straight Gain
It is the necessary value for the generated parallel line to cross the graph and thus it is possible to locate the elastic limit.
Extensometer
Extensometer 1: Select the indicated strain extensometer model, if available.
Extensometer 2: Select the indicated strain extensometer model, if available.
Test options
Tension (MPa) X Deformation (%): Test option as graph of tension in MPa and Deformation in %.
Force (N) X Position (mm): Test option as graph of N-Force and Position (stratching) in mm.
Indicators
Strength (N): Select the Strength indicator in the analysis of the results:
Posição (mm): Seleciona o indicador de Posição na análise dos resultados:
Position (mm): Select the Position indicator in the analysis of the results:
Tensão Máxima (MPa): Seleciona o indicador de Tensão Máxima na análise dos resultados:
Maximum tension (MPa): Selects the Maximum tension indicator in the analysis of the results:
Yield stress (MPa): Select the Runoff tension indicator in the analysis of the results:
Stretching (%): Selects the Stretching indicator in the analysis of the results:
Area Reduction (%): Selects the Area Reduction indicator in the analysis of the results:
Young’s Modulus: Selects the Young’s Modulus indicator in the analysis of the results:
Automatic Stop
Power Drop Stop: Parameterizes the percentage of power drop necessary to interrupt the test, when reaching the specified percentage the test is finished.
Maximum Force Stop: Parameterization of the maximum force desired for the test, when reaching the specified force the test will be completed;
Displacement Stop: Parameterization of the desired displacement for the test, upon reaching the specified displacement the test will be completed;
Pause the displacement: Parameterization of specific displacement for the test pause.
TEST TAB
Test tabs: These are used to store information about the test performed. If the operator wishes to perform more than one test, he must select a new test tab (Ex: Test 2, Test 3 …), up to 10 consecutive tests can be performed.
Young´s Modulus 1: Young´s Modulus Indicator
Position 1: Home position indicator
Force 1: Shape Indicator
Tension 1: tension indicator
LF 1: Final stretch indicator
Stretch 1: Stretch indicator
AF 1: Final stretch indicator
Area Reduction: Area reduction indicator
A. Transversal 1: Transverse area indicator
T. Flow 1: Flow tension indicator
Test results graph: Displays graph of the test performed
Pause button: Use the “Pause” button to pause the test and disable it to resume the test.
Stop button: The test can be interrupted by clicking on the “Stop Test” button
Graphic reset button: Clears the graphic information that you no longer want to use.
Reset Force button: Reset the strength value of the Indicator.
Reset Position button: Reset the Position value.
Export Chart: Click on the chart with the right mouse button, Export / Export Data To Excel.
REPORT TAB
In the upper left part of the report it is possible to change all the information.
It is possible to insert in the reports all of the data referring to the company that is carrying out the test as registration data, logo, address, cnpj, email, etc.
In the upper right part of the report, it is possible to change all information.
Test:
Standard:
Identification:
Load cell:
Travel Speed:
Temperature:
Date:
Time:
Test performed:
Pre load:
Relative humidity:
Machine used:
Test result indicators:
Samples:
Maximum Force (N):
Maximum Position (mm):
Maximum Tension (Mpa)
Yield Tension (MPa)
Yield Stress (MPa)
Area Reduction:
Young’s modulus:
Minimum value:
Maximum Value
Medium Value
Standard deviation:
Saving the report:
1. In the “Export Address” field, click on the folder.
2. Find the location where you want to save your reports.
3. Insert a name and click “OK”
4. On the bottom right click on “Export”
Ready, your report has been saved to the address indicated.
Stress–strain curve
The stress-strain curve of the tested samples is displayed, for the graph to be displayed it is necessary to select the tested sample from 1 to 10, more than one sample can be selected at the same time.
PARAMETERS TAB
The parameterization and calibration data of the equipment are presented, being used only in cases where they need technical assistance from BIOPDI, not being used for changes to the user of the equipment.
USERS TAB
The software has a security system with user levels (Super Administrator, Administrator, Supervisor and Operator), which can be registered and configured with passwords and protection options, allowing the equipment to have the usage history of each user.
Tensile Testing Machine:
Videos about Materials Testing
Tensile Testing Machine:
Standards for Materials Testing
Here are some of the most commonly used international standards, both ISO (International Organization for Standardization) and ASTM (American Society for Testing and Materials), for various types of material testing.
For other types of standards, consult our team.
Tensile Test:
- ISO 6892-1: Metallic materials – Tensile testing – Part 1: Method of test at room temperature
- ISO 6892-2: Metallic materials – Tensile testing – Part 2: Method of test at elevated temperature
- ISO 527-2: Plastics – Determination of tensile properties – Part 2: Test conditions for moulding and extrusion plastics
- ISO 37: Rubber, vulcanized or thermoplastic – Determination of tensile stress-strain properties
- ASTM E8/E8M: Standard Test Methods for Tension Testing of Metallic Materials
- ASTM D638: Standard Test Method for Tensile Properties of Plastics
- ASTM A370: Standard Test Methods and Definitions for Mechanical Testing of Steel Products
- ASTM D412: Standard Test Methods for Vulcanized Rubber and Thermoplastic Elastomers—Tension
- ASTM F606/F606M: Standard Test Methods for Determining the Mechanical Properties of Externally and Internally Threaded Fasteners, Washers, Direct Tension Indicators, and Rivets
- ASTM D3039/D3039M: Standard Test Method for Tensile Properties of Polymer Matrix Composite Materials
Compression Test:
- ISO 604: Plastics – Determination of compressive properties
- ISO 844: Rigid cellular plastics – Determination of compression properties
- ISO 12192: Paper and board — Determination of compressive strength — Ring crush method
- ISO 9933: Rubber- or plastics-coated fabrics — Determination of resistance to compression
- ASTM E9: Standard Test Methods of Compression Testing of Metallic Materials at Room Temperature
- ASTM D695: Standard Test Method for Compressive Properties of Rigid Plastics
- ASTM D1621: Standard Test Method for Compressive Properties Of Rigid Cellular Plastics
- ASTM D575: Standard Test Methods for Rubber Properties in Compression
- ASTM C365/C365M: Standard Test Method for Flatwise Compressive Properties of Sandwich Cores
- ASTM D2412: Standard Test Method for Determination of External Loading Characteristics of Plastic Pipe by Parallel-Plate Loading
- Shear Test:
- ISO 14130: Fibre-reinforced plastic composites – Determination of apparent interlaminar shear strength by short-beam method
- ISO 4587: Adhesives — Determination of tensile lap-shear strength of bonded assemblies
- ISO 11003-2: Adhesives — Determination of shear behaviour of structural adhesives
- ISO 19252: Jewellery — Determination of resistance to impact for gemstones — Impulse hammer test with shear impact
- ASTM D732: Standard Test Method for Shear Strength of Plastics by Punch Tool
- ASTM D5379/D5379M: Standard Test Method for Shear Properties of Composite Materials by the V-Notched Beam Method
- ASTM D7078/D7078M: Standard Test Method for Shear Properties of Composite Materials by V-Notched Rail Shear Method
- ASTM D1002: Standard Test Method for Apparent Shear Strength of Single-Lap-Joint Adhesively Bonded Metal Specimens by Tension Loading (Metal-to-Metal)
- ASTM D2719: Standard Test Methods for Wood Structural Panels in Shear Through-the-Thickness
- ASTM D3846: Standard Test Method for In-Plane Shear Strength of Reinforced Plastics
Bend Test:
- ISO 7438: Metallic materials — Bend test
- ISO 178: Plastics — Determination of flexural properties
- ISO 14125: Fibre-reinforced plastic composites — Determination of flexural properties
- ISO 15113: Plastics — Film and sheeting — Determination of tear resistance
- ASTM E290: Standard Test Methods for Bend Testing of Material for Ductility
- ASTM D790: Standard Test Methods for Flexural Properties of Unreinforced and Reinforced Plastics and Electrical Insulating Materials
- ASTM A370: Standard Test Methods and Definitions for Mechanical Testing of Steel Products
- ASTM D6272: Standard Test Method for Flexural Properties of Unreinforced and Reinforced Plastics and Electrical Insulating Materials by Four-Point Bending
- ASTM D522: Standard Test Methods for Mandrel Bend Test of Attached Organic Coatings
- ASTM D2344/D2344M: Standard Test Method for Short-Beam Strength of Polymer Matrix Composite Materials and Their Laminates
Flexural Test:
- ISO 178: Plastics — Determination of flexural properties
- ISO 14125: Fibre-reinforced plastic composites — Determination of flexural properties
- ISO 14126: Fibre-reinforced plastic composites — Determination of compressive properties in the in-plane direction
- ISO 17892-5: Geotechnical investigation and testing — Laboratory testing of soil — Part 5: Incremental loading oedometer test
- ASTM D790: Standard Test Methods for Flexural Properties of Unreinforced and Reinforced Plastics and Electrical Insulating Materials
- ASTM D6272: Standard Test Method for Flexural Properties of Unreinforced and Reinforced Plastics and Electrical Insulating Materials by Four-Point Bending
- ASTM D7249/D7249M: Standard Test Method for Facing Properties of Sandwich Constructions by Long Beam Flexure
- ASTM C393/C393M: Standard Test Method for Core Shear Properties of Sandwich Constructions by Beam Flexure
- ASTM D7264/D7264M: Standard Test Method for Flexural Properties of Polymer Matrix Composite Materials
- ASTM C78/C78M: Standard Test Method for Flexural Strength of Concrete (Using Simple Beam with Third-Point Loading)
Peel Test:
- ISO 8510-2: Adhesives — Peel test for a flexible-bonded-to-rigid test specimen assembly — Part 2: 180 degree peel
- ISO 4578: Adhesives — Determination of peel resistance of high-strength adhesive bonds
- ASTM D1876: Standard Test Method for Peel Resistance of Adhesives (T-Peel Test)
- ASTM D3330/D3330M: Standard Test Method for Peel Adhesion of Pressure-Sensitive Tape
- ASTM F88/F88M: Standard Test Method for Seal Strength of Flexible Barrier Materials
Tear Test:
- ISO 6383-2: Plastics – Film and sheeting – Determination of tear resistance – Part 2: Elmendorf method
- ISO 34-1: Rubber, vulcanized or thermoplastic – Determination of tear strength – Part 1: Trouser, angle and crescent test pieces
- ASTM D624: Standard Test Method for Tear Strength of Conventional Vulcanized Rubber and Thermoplastic Elastomers
- ASTM D2261: Standard Test Method for Tearing Strength of Fabrics by the Tongue (Single Rip) Procedure (Constant-Rate-of-Extension Tensile Testing Machine)
- ASTM D1424: Standard Test Method for Tearing Strength of Fabrics by Falling-Pendulum (Elmendorf-Type) Apparatus
Friction Test:
- ISO 8295: Plastics – Film and sheeting – Determination of the coefficients of friction
- ISO 15359: Paper and board – Determination of the static and kinetic coefficients of friction – Horizontal plane method
- ASTM D1894: Standard Test Method for Static and Kinetic Coefficients of Friction of Plastic Film and Sheeting
- ASTM G115: Standard Guide for Measuring and Reporting Friction Coefficients
- ASTM G99: Standard Test Method for Wear Testing with a Pin-on-Disk Apparatus (This can sometimes be used to determine friction)
Bond Test:
- ISO 4624: Paints and varnishes – Pull-off test for adhesion
- ISO 10373-1: Cards and security devices for personal identification – Test methods – Part 1: General characteristics
- ASTM D4541: Standard Test Method for Pull-Off Strength of Coatings Using Portable Adhesion Testers
- ASTM D905: Standard Test Method for Strength Properties of Adhesive Bonds in Shear by Compression Loading
- ASTM D906: Standard Test Method for Strength Properties of Adhesives in Plywood Type Construction in Shear by Tension Loading
Fracture Test:
- ISO 13586: Plastics – Determination of fracture toughness (GIC and KIC) – Linear elastic fracture mechanics (LEFM) approach
- ISO 12135: Metallic materials – Unified method of test for the determination of quasistatic fracture toughness
- ASTM E399: Standard Test Method for Linear-Elastic Plane-Strain Fracture Toughness KIC of Metallic Materials
- ASTM E1820: Standard Test Method for Measurement of Fracture Toughness
- ASTM D5045: Standard Test Methods for Plane-Strain Fracture Toughness and Strain Energy Release Rate of Plastic Materials
Indentation Test:
- ISO 14577-1: Metallic materials – Instrumented indentation test for hardness and materials parameters – Part 1: Test method
- ISO 6507-1: Metallic materials – Vickers hardness test – Part 1: Test method
- ASTM E384: Standard Test Method for Microindentation Hardness of Materials
- ASTM E18: Standard Test Methods for Rockwell Hardness of Metallic Materials
- ASTM D2240: Standard Test Method for Rubber Property-Durometer Hardness
Puncture Test:
- ISO 6603-2: Plastics – Determination of puncture impact behaviour of rigid plastics – Part 2: Instrumented impact testing
- ISO 7765-1: Plastics film and sheeting – Determination of impact resistance by the free-falling dart method – Part 1: Staircase methods
- ASTM D3763: Standard Test Method for High Speed Puncture Properties of Plastics Using Load and Displacement Sensors
- ASTM D4833/D4833M: Standard Test Method for Index Puncture Resistance of Geomembranes and Related Products
- ASTM D1709: Standard Test Methods for Impact Resistance of Plastic Film by the Free-Falling Dart Method
Crush Resistance Test:
- ISO 7263: Corrugated fibreboard — Creasing and cutting — Determination of the force to bend and of the bending quality
- ISO 3037: Corrugated fibreboard — Determination of edgewise crush resistance
- ASTM D642: Standard Test Method for Determining Compressive Resistance of Shipping Containers, Components, and Unit Loads
- ASTM D4179: Standard Test Method for Single Pellet Crush Strength of Formed Catalyst Shapes
- ASTM D6175: Standard Test Method for Radial Crush Strength of Extruded Catalyst and Catalyst Carrier Particles
Axial Torsion Test:
- ISO 7800: Metallic materials — Wire — Simple torsion test
- ISO 9649: Metallic materials — Wire — Reverse torsion test
- ASTM E143: Standard Test Method for Shear Modulus at Room Temperature
- ASTM F543: Standard Specification and Test Methods for Metallic Medical Bone Screws
- ASTM D5279: Standard Test Method for Plastics: Dynamic Mechanical Properties: In Torsion
Dynamic Test:
- ISO 12110-1: Metallic materials — Fatigue testing — Variable amplitude fatigue testing — Part 1: General principles, test method and reporting requirements
- ISO 4664-1: Rubber, vulcanized or thermoplastic — Determination of dynamic properties — Part 1
- ASTM D5026: Standard Test Method for Plastics: Dynamic Mechanical Properties: In Tension
- ASTM D4065: Standard Practice for Plastics: Dynamic Mechanical Properties: Determination and Report of Procedures
Extensometry and strain measurement
- ISO 9513: Metallic materials — Calibration of extensometers used in uniaxial testing.
- ISO 527-1: Plastics — Determination of tensile properties — Part 1: General principles. (This standard includes the use of extensometers for measuring elongation)
- ASTM E83: Standard Practice for Verification and Classification of Extensometer Systems.
- ASTM E399: Standard Test Method for Linear-Elastic Plane-Strain Fracture Toughness KIC of Metallic Materials. (This standard makes extensive use of extensometers)
- ASTM E8/E8M: Standard Test Methods for Tension Testing of Metallic Materials. (In these test methods, the use of extensometers is required to determine certain properties)
Load cells
- ISO 376: Metallic materials — Calibration of force-proving instruments used for the verification of uniaxial testing machines. (This standard includes provisions for calibrating load cells.)
- ASTM E74: Standard Practice for Calibration of Force-Measuring Instruments for Verifying the Force Indication of Testing Machines. (This standard involves calibrating load cells.)
- ASTM E251: Standard Test Methods for Performance Characteristics of Metallic Bonded Resistance Strain Gauges. (While not strictly about load cells, this standard covers the strain gauges that are used in many load cells.)
- ISO 7500-1: Metallic materials — Calibration and verification of static uniaxial testing machines — Part 1: Tension/compression testing machines — Calibration and verification of the force-measuring system. (This standard includes calibration of load cells.)
- ASTM E4: Standard Practices for Force Verification of Testing Machines. (This standard provides practices for verifying the forces exerted by testing machines and covers the use of load cells.)
What is a Tensile Testing Machine?
A tensile testing machine is a mechanical testing apparatus used extensively in the field of material science and engineering. Its primary purpose is to apply a uniaxial tension load, or a force that stretches an object, to a test specimen, and then measure the response of the material.
A tensile testing machine is a fundamental piece of equipment in the field of materials science and engineering. It’s designed to subject materials to tensile or pull forces to determine their strength, durability, and elasticity.
The purpose of a tensile testing machine is to measure the mechanical properties of materials under uniaxial tensile stress. These properties include the material’s ultimate tensile strength, yield strength, elongation, and reduction of area.
The tensile testing process involves securing a sample of the material within the machine’s grips, which are positioned in a vertical manner. The machine then applies an increasing load on the material, pulling it apart until it fractures or breaks. The machine records the force applied and the material’s response, often in the form of a stress-strain curve.
The ultimate tensile strength (UTS) is the maximum stress that a material can withstand while being stretched or pulled before breaking. Yield strength is the stress at which a material begins to deform plastically, meaning it won’t return to its original shape after the load is removed. Elongation measures the degree to which the material can be stretched before breaking, and reduction of area is an indicator of a material’s ductility.
Tensile testing machines are widely used across many industries, including but not limited to, construction, aerospace, automotive, and materials manufacturing. They are critical in product development and quality control, as they allow engineers to understand a material’s suitability for specific applications based on its tensile properties.
What is the importance of a Tensile Testing Machine?
The importance of a tensile testing machine in material science and engineering cannot be overstated. It plays an integral role in ensuring the safety, reliability, and longevity of a myriad of products and structures we use every day.
- Understanding Material Properties: A tensile testing machine is a key tool for determining the mechanical properties of a material, such as its yield strength, ultimate tensile strength, elongation, and reduction of area. This data provides insight into the material’s durability, ductility, elasticity, and resistance to deformation, all of which are critical for assessing its performance under various conditions.
- Quality Control: Industries such as automotive, aerospace, construction, and manufacturing utilize tensile testing machines for quality control. By testing materials during different stages of production, manufacturers can ensure their products meet the necessary safety and performance standards.
- Research & Development: In the development of new materials or the improvement of existing ones, tensile testing provides valuable data that helps researchers understand how a material behaves under tension. This can lead to the creation of materials with enhanced properties tailored to specific applications.
- Material Selection: The data from tensile testing assists engineers and designers in choosing the right material for a particular application. For instance, a material with a high yield strength might be chosen for a load-bearing structure, whereas a material with high ductility might be preferable for an application that requires flexibility.
- Failure Analysis: When a material or component fails or breaks, a tensile testing machine can be used to determine the cause of the failure. This helps to prevent future occurrences and improve the design or material selection process.
- Regulatory Compliance: In many sectors, materials must meet specific regulatory standards to ensure safety and performance. Tensile testing is a key method for demonstrating that these standards are met.
The tensile testing machine is a cornerstone of modern materials science and engineering, enabling the analysis and understanding of materials’ tensile properties, supporting quality control efforts, facilitating the development of innovative materials, aiding in appropriate material selection, helping in failure analysis, and ensuring regulatory compliance.
What are the advantages of using a Tensile Testing Machine?
The use of a tensile testing machine presents a multitude of advantages in the field of materials science and engineering. Here are some of the key benefits:
- Detailed Material Analysis: Tensile testing machines provide comprehensive data about a material’s mechanical properties, including yield strength, ultimate tensile strength, elongation, and reduction of area. This information is essential in understanding how a material behaves under stress, its durability, ductility, and overall performance.
- Accuracy and Precision: Modern tensile testing machines deliver highly accurate and precise measurements due to their advanced technology and automation. This allows for consistent testing conditions and reliable data.
- Versatility: Tensile testing machines can be used to test a wide range of materials, including metals, polymers, composites, ceramics, and more. This makes them versatile tools in various industries and research environments.
- Predictive Insights: The data obtained from tensile testing machines can help predict how a material will perform under certain conditions. This is especially useful in industries like construction, automotive, aerospace, and more where safety and durability are paramount.
- Product Development: In the research and development phase, tensile testing machines provide critical data that helps in the development of new materials or improving existing ones. The insights derived can drive innovation and performance improvements.
Tensile testing machines are invaluable in understanding the characteristics of various materials under tensile stress. The data they generate not only influences the selection of materials for different applications but also drives innovation, maintains quality, ensures safety standards, and facilitates regulatory compliance.
How does a Tensile Testing Machine work?
A tensile testing machine, also known as a universal testing machine (UTM), operates by applying a controlled tensile (pulling) force to a material and measuring the material’s response to the stress. The steps in its operation are as follows:
- Preparation of the Test Specimen: First, a sample of the material to be tested is prepared. This sample, or test specimen, is usually rod-like or flat with standardized dimensions, depending on the material type and the specific standard being followed.
- Mounting the Specimen: The prepared specimen is then securely mounted within the grips of the tensile testing machine. The grips are designed to hold the sample firmly without causing pre-test damage. The position of the specimen is usually vertical, but can vary based on the testing setup.
- Application of Load: Once the specimen is properly mounted, the machine applies a tensile load to it. This is achieved by moving the grips apart at a constant rate, gradually stretching the material. The applied load and rate of loading are carefully controlled and monitored.
- Data Collection: As the tensile load is applied, the machine measures the amount of force being exerted and the resulting elongation (stretching) of the specimen. Modern tensile testing machines use sophisticated sensors and software to capture this data with high precision.
- Data Analysis: The collected data is used to plot a stress-strain curve, a graph that shows the material’s response to the applied stress. From this curve, critical mechanical properties of the material such as the yield strength, ultimate tensile strength, modulus of elasticity, and elongation can be determined.
- Result Interpretation: The final step involves interpreting the results and drawing conclusions about the material’s tensile properties. These properties are integral in understanding the material’s performance under tension, informing decisions about its use in specific applications.
The working principle of a tensile testing machine is the application of a controlled tensile load to a material and the precise measurement of the material’s response. This data provides invaluable insights into the material’s mechanical properties and its suitability for various applications.
Parts and components of a Tensile Testing Machine
A tensile testing machine, often referred to as a Universal Testing Machine (UTM), consists of several primary parts and components, each playing a crucial role in its function. Here are the key components:
- Frame: The frame is the main structure of the machine, which houses and supports all other components. It often consists of one or two vertical columns, and is designed to withstand high loads.
- Loading System: The loading system applies the force to the specimen. Depending on the machine design, this could be a hydraulic system, a screw-driven system, or an electromechanical system.
- Grips or Jaws: The grips or jaws are used to hold the test specimen in place during the test. They need to be strong enough to hold the specimen securely without slipping, and without applying so much pressure that the specimen is damaged. Different types of grips may be used depending on the material being tested.
- Load Cell: The load cell is a type of transducer that measures the force applied to the test specimen. It converts the force into an electrical signal, which is then interpreted by the machine’s control system.
- Extensometer: An extensometer measures the change in length (or strain) of the specimen as it is being pulled. This is essential for determining material properties like elongation and yield strength.
- Crosshead: The crosshead is the moving component of the machine that applies the tensile load to the test specimen. In many machines, the speed of the crosshead can be precisely controlled.
- Control System: The control system regulates the operation of the machine, such as the speed of testing and load application. It also collects and interprets data from the load cell and extensometer.
- Software: Modern tensile testing machines are often computerized, using software to control the machine’s operation, record data, and perform calculations. The software typically provides a user-friendly interface and enables data analysis, storage, and reporting.
These components allow a tensile testing machine to perform its essential function: to apply a controlled tensile force to a material, measure the material’s response, and provide data on its mechanical properties.
The procedures performed to use the Tensile Testing Machine
The operation of a tensile testing machine involves several key procedures. Here is a step-by-step breakdown of the general process:
- Specimen Preparation: The first step is to prepare the material sample, or test specimen, according to the relevant testing standards. This may involve cutting or shaping the material into a specific form, usually a rod or flat strip, with predetermined dimensions.
- Mounting the Specimen: Next, the specimen is securely placed in the grips or jaws of the tensile testing machine. It’s crucial to ensure the specimen is mounted straight and uniform to prevent irregular force distribution.
- Machine Setup: Set the parameters for the test on the machine’s control system. This includes the rate at which the load is applied (strain rate), the maximum load, and other test-specific settings. The load cell and extensometer suitable for the test are also selected at this stage.
- Initiating the Test: Once everything is set up, the test can be started. The machine will begin to apply a tensile (pulling) force to the specimen at the preset rate.
- Data Collection: As the test proceeds, the machine measures the force applied (from the load cell) and the resulting deformation or change in length of the specimen (from the extensometer). This data is usually automatically recorded by the machine’s software.
- Test Completion: The test continues until the specimen breaks or the desired strain is reached. At this point, the machine will automatically stop applying force.
- Data Analysis: The collected data is used to generate a stress-strain curve, which graphically represents the material’s response to the applied force. Key material properties, such as the yield strength, ultimate tensile strength, and elongation, are calculated from this curve.
- Report Generation: Finally, a test report is generated. This report typically includes details of the test procedure, the resulting stress-strain curve, calculated material properties, and any observations made during the test.
Throughout this process, it’s crucial to follow all safety procedures and guidelines to ensure the test is carried out safely. Also, to obtain accurate results, it’s important to ensure the machine is regularly calibrated and maintained.
Data obtained in the Tensile Testing Machine
A tensile testing machine yields a wealth of data about a material’s mechanical properties under tensile stress. Here are some of the key data points that can be obtained:
- Stress-Strain Curve: One of the primary outputs of a tensile test is the stress-strain curve. This graph represents how a material responds to the applied stress, showing the relationship between the applied force (stress) and the deformation or change in length (strain) of the material. The curve can reveal various stages of the material’s behavior, such as the elastic region, yield point, and plastic deformation region.
- Elastic Modulus (Young’s Modulus): This is a measure of the stiffness of a material within the elastic region (the initial linear portion of the stress-strain curve), where the material returns to its original shape after the stress is removed. It’s calculated as the ratio of stress to strain within this region.
- Yield Strength: This is the stress at which a material begins to deform plastically. Beyond this point, the material will not return to its original shape once the load is removed. On a stress-strain curve, it’s typically where the linear (elastic) part of the curve ends and the curve starts to flatten.
- Ultimate Tensile Strength (UTS): This is the maximum stress that a material can withstand while being stretched before failure. It corresponds to the highest point on the stress-strain curve.
- Elongation: This is a measure of a material’s ductility, or its ability to deform under tensile stress without breaking. It’s often presented as a percentage, representing the change in length of the specimen from its original length to its length at the point of failure.
- Reduction of Area: This value represents the decrease in cross-sectional area of the specimen at the point of failure, compared to its original area. It’s another measure of a material’s ductility.
- Resilience and Toughness: Resilience is the capacity of a material to absorb energy within the elastic region, while toughness is the material’s ability to absorb energy up to the point of fracture. These can be calculated as the areas under the stress-strain curve.
These data points can provide invaluable insights into the tensile properties of a material, helping to determine its suitability for specific applications, enabling the design of safe and effective products, and contributing to the advancement of material science and engineering.
Types of samples/specimens used in the Tensile Testing Machine
The types of samples or specimens used in a tensile testing machine can vary widely, depending on the material being tested and the specific application or testing standard. Despite this diversity, most tensile specimens share a common feature: they are designed to have a uniform, narrow section where failure will occur. Here are a few common types:
- Dog-bone Shaped Specimens: This is a common shape for tensile testing specimens, especially for metals and polymers. The “dog-bone” shape is wider at the ends and narrower in the middle. This design encourages the specimen to break in the middle (the gauge section) during testing, ensuring a uniform distribution of stress.
- Flat Specimens: These specimens are used in the testing of sheet materials, like thin metals and polymers. They are often similar in shape to dog-bone specimens but are flat and thin.
- Round or Cylindrical Specimens: These are often used for testing metals and other hard materials. The cylindrical shape allows for uniform stress distribution along the gauge length.
- Threaded Specimens: These are used when testing bolts, screws, or other threaded components. The threaded ends allow them to be securely gripped by the testing machine.
- Full-Size Product Specimens: In some cases, the actual product or component, such as a wire, cable, or rebar, is tested. This can provide more accurate information about the product’s performance in real-world conditions.
- Micro-Specimens: These small-sized specimens are used in micro-tensile testing, often for biological materials, microelectronic components, thin films, and other small-scale applications.
The size, shape, and preparation of tensile testing specimens are often defined by specific standards, such as those set by ASTM International, ISO, or other standardization bodies. The choice of specimen type depends on the material being tested, the properties of interest, and the specific requirements of the test.
Additional information about Tensile Testing Machine
The tensile testing machine, while straightforward in its primary function—applying tensile force and measuring a material’s response—has a number of additional aspects and features that make it an invaluable tool in many fields of study and industry. Here are some additional points of interest:
- Variety of Machines: Tensile testing machines come in various sizes and capacities, from small bench-top machines for testing tiny or delicate specimens, to large floor-standing machines capable of exerting enormous forces for testing high-strength materials or large components.
- Standards Compliance: Tensile tests are usually carried out according to specific standards, such as those established by ASTM International, ISO, or other organizations. These standards specify the method of testing, including specimen preparation, test setup, and data interpretation, ensuring consistency and comparability of results.
- Environment Simulation: Some advanced tensile testing machines can simulate various environmental conditions during the test, such as high or low temperatures, humidity, or corrosive environments. This can provide valuable information about a material’s behavior under real-world conditions.
- Additional Measurements: While the primary measurements in a tensile test are the applied force and the resulting deformation, some tensile testing machines can also measure other parameters, such as temperature, strain rate, or acoustic emissions, providing further insights into the material’s behavior.
- Advanced Analysis Capabilities: Modern tensile testing machines often come with sophisticated software that not only controls the test and records data, but also offers a range of analysis tools. This can include the calculation of material properties, generation of stress-strain curves, statistical analysis, and more.
- Maintenance and Calibration: To ensure accurate and reliable results, tensile testing machines must be properly maintained and regularly calibrated. Calibration typically involves applying known loads to the machine and checking that it measures these loads accurately.
- Safety Considerations: Operating a tensile testing machine involves the application of high forces and can result in the sudden fracture of specimens. Therefore, safety measures, such as the use of safety shields and proper operator training, are crucial.
- Future Developments: As materials science advances and new materials are developed, the requirements for tensile testing also evolve. Future developments in tensile testing machines may include greater capacity, higher precision, more advanced analysis capabilities, and the ability to simulate more complex environmental conditions.
By understanding these additional aspects of tensile testing machines, users can make the most of this powerful tool, obtaining accurate, reliable, and relevant data about their materials.
Types of materials tested on the Tensile Testing Machine
Tensile testing machines are used to evaluate the mechanical properties of a wide range of materials, including metals, polymers, ceramics, and composites. Here’s an overview of these different types of materials and some common examples:
Metals:
Metals are materials known for their ability to conduct heat and electricity, their malleability and ductility. They are also often characterized by their luster, or shiny appearance.
- Steel: An alloy of iron with small amounts of carbon, steel is admired for its high tensile strength and durability. Its Young’s modulus is about 200 GPa, with a tensile strength that ranges from 500-1400 MPa, a shear modulus of 80 GPa, and elongation in the 15-25% range.
- Aluminum: A lightweight metal, aluminum is recognized for its resistance to corrosion and excellent strength-to-weight ratio. Its Young’s modulus stands at 69 GPa, with a tensile strength of 40-500 MPa, a shear modulus of 26 GPa, and elongation ranging from 10-25%.
- Titanium: A strong, light, and corrosion-resistant metal, titanium is often used in aircraft, missiles, and spacecraft. Its low density makes it perfect for these applications where weight is critical. Titanium has a Young’s modulus of about 116 GPa, a tensile strength ranging from 240-370 MPa, a shear modulus of 44 GPa, and elongation from 10-25%.
- Copper: Known for its excellent electrical conductivity, copper is widely used in electrical wires and cables. Besides, its high thermal conductivity makes it perfect for heat exchangers. Copper’s Young’s modulus is about 110 GPa, its tensile strength ranges from 210-420 MPa, it has a shear modulus of 48 GPa, and elongation from 10-60%.
Polymers:
Polymers are a type of material composed of long, repeating chains of molecules. They are characterized by their light weight and resistive properties.
- Polyethylene (PE): A common plastic known for its chemical resistance, PE has a Young’s modulus of 0.1-1.5 GPa, a tensile strength of 10-40 MPa, and can elongate between 200-700% before breaking.
- Polypropylene (PP): PP is another commonly used plastic known for its toughness and flexibility. It has a Young’s modulus of 1.5-2 GPa, a tensile strength of 25-40 MPa, and can elongate 100-600%.
- Polystyrene (PS): Often used in disposable cutlery, CD cases, and other consumer goods, polystyrene is a versatile plastic known for its rigidity and clarity. Its Young’s modulus is about 3-3.5 GPa, tensile strength is between 35-55 MPa, and it typically elongates 1-4% before breaking.
- Polyvinyl Chloride (PVC): PVC is a common plastic used in construction because it’s cheap, durable, and easy to assemble. It’s used for everything from pipes and cable insulation to clothing and inflatable structures. PVC has a Young’s modulus of 2-4 GPa, a tensile strength of 40-80 MPa, and elongation from 20-40%.
Ceramics:
Ceramics are hard, brittle materials typically used for their high melting points and electrical insulation properties.
- Alumina (Al2O3): Alumina is a ceramic material known for its excellent thermal and electrical insulation properties. It has a Young’s modulus of 380-400 GPa, a tensile strength of 200-400 MPa, and a shear modulus of 152 GPa.
- Zirconia (ZrO2): Zirconia is a high-strength, tough ceramic with a Young’s modulus of 200-250 GPa, a tensile strength of 800-1000 MPa, and a shear modulus of 80-90 GPa.
- Silicon Carbide (SiC): Known for its hardness and resistance to wear, Silicon Carbide is used in applications like car brakes, bulletproof vests, and even astronomical telescope mirrors. It has a Young’s modulus of 400-430 GPa, a tensile strength of 350-650 MPa, a shear modulus of 180 GPa, and virtually no elongation at break.
- Boron Carbide (B4C): This ceramic material is known for its extreme hardness and is used in body armor, abrasives, and neutron absorbers in nuclear reactors. Boron Carbide has a Young’s modulus of 450-470 GPa, a tensile strength of 300-350 MPa, a shear modulus of 175 GPa, and virtually no elongation at break.
Composites:
Composite materials are made from two or more different types of materials, which allows them to possess qualities of both.
- Carbon Fiber Reinforced Polymer (CFRP): CFRP is a strong, lightweight composite material with a Young’s modulus of 70-155 GPa, a tensile strength of 1000-1500 MPa, a shear modulus of 5-10 GPa, and an elongation of 1-2%.
- Glass Fiber Reinforced Polymer (GFRP): GFRP, similar to CFRP but reinforced with glass fibers, has a Young’s modulus of 40-45 GPa, a tensile strength of 1000-1500 MPa, a shear modulus of 15-20 GPa, and an elongation of 2-5%.
- Fiber-Reinforced Plastic (FRP): Commonly used in the aerospace, automotive, and marine industries for its high strength-to-weight ratio, FRP has a Young’s modulus of 20-30 GPa, a tensile strength of 500-1500 MPa, and elongation of 2-5%.
- Kevlar-Epoxy Composites: Often used in bulletproof vests and other protective clothing, this composite material is admired for its lightweight and high strength properties. Kevlar-epoxy composites have a Young’s modulus of 70-130 GPa, a tensile strength of 1000-1400 MPa, and an elongation of 2-3%.
FAQ
What is a tensile testing machine?
A tensile testing machine, also known as a tension test machine or universal testing machine, is a sophisticated device engineered to test the mechanical properties of materials under tensile or pulling stress conditions. By subjecting materials to controlled tension until failure, it helps determine various critical parameters such as tensile strength, elongation, yield strength, and modulus of elasticity, providing essential information about a material’s ability to perform in specific applications.
How much is a tension testing machine?
The cost of a tensile testing machine can vary widely depending on several factors, including the maximum load capacity, the level of automation, the precision of the measurements, the brand, and any additional features or accessories. Basic tabletop models can cost a few thousand dollars, while high-capacity, fully automated systems with advanced software control can exceed $50,000.
What is a tensile machine used for?
A tensile machine is primarily used to evaluate the mechanical properties of materials under tensile load. These properties include tensile strength (the maximum stress a material can withstand before breaking), yield strength (the stress at which a material begins to deform plastically), and elongation (how much a material can be stretched before breaking). It is used across a multitude of sectors such as construction, automotive, aerospace, and material manufacturing to ensure that materials meet the necessary standards for safety and performance.
What are the different types of tensile machines?
Different types of tensile testing machines include universal testing machines, which can perform tensile, compression, bending, and shear tests; electromechanical testing machines, which use an electric motor to apply force; and servo-hydraulic testing machines, which use hydraulic power for testing. The choice depends on factors like the type of material being tested, the precision required, and the specific testing standards to be followed.
How do you run a tensile test?
To perform a tensile test, a sample (or specimen) of the material is prepared according to specific standards, typically in a “dog-bone” shape. This specimen is then secured in the machine’s grips, and a tensile load is applied at a predetermined rate. The load is increased until the specimen fails or breaks. Throughout the test, the machine records the force applied and the resulting displacement or stretch of the material, which is then used to calculate its tensile properties.
What are the benefits of tensile testing?
Tensile testing provides invaluable insights into a material’s mechanical properties and deformation behavior. Understanding these properties can help engineers select the most suitable materials for a specific application, predict a material’s performance under load, and identify any potential issues or weaknesses in a material that could lead to premature failure. It also ensures compliance with industry and international standards, enhancing product safety and reliability.
How do you measure tensile strength at home?
Measuring tensile strength at home without professional equipment is challenging. However, simple experiments can be done with readily available materials. For instance, you can hang increasing weights from a rubber band until it breaks, measuring the length of the rubber band at each stage. This won’t provide an exact tensile strength but can give an understanding of how materials stretch and eventually break under tensile stress.
What machines measure tensile strength?
Tensile strength is typically measured using a tensile testing machine or universal testing machine. These machines apply a progressively increasing tensile load to a specimen until it fractures, measuring the force applied and the specimen’s deformation throughout the test.
What is tensile vs compressive test?
Tensile testing and compressive testing are two key methods of determining a material’s mechanical properties. Tensile testing measures a material’s resistance to forces that attempt to pull it apart or stretch it, while compressive testing measures a material’s ability to resist forces that try to squeeze or compact it. While the same material can exhibit different tensile and compressive strengths, both tests provide valuable insights into a material’s behavior under different stress conditions.
What is the standard for tensile testing?
Tensile testing standards vary depending on the material and the industry. ASTM International and ISO provide widely accepted testing standards. For instance, ASTM E8 is a standard for tension testing of metallic materials. It specifies the specimen’s dimensions, testing procedures, and data analysis methods to ensure consistent, reliable results.
What is the tensile test for steel?
In a tensile test for steel, a steel sample is clamped into a testing machine and pulled until it fractures. The test measures the steel’s yield strength (the point at which the steel starts to deform plastically), tensile strength (the maximum amount of stress that the steel can withstand), and elongation (the amount of stretch the steel experiences before breaking).
What do you mean by tensile strength?
Tensile strength is a mechanical property of materials that describes the maximum amount of tensile (pulling) stress that a material can endure before breaking or failing. It is typically measured in units of force per cross-sectional area (for example, pounds per square inch or Pascals). Higher tensile strength indicates a material’s greater ability to withstand tensile stress without failure.
How does a universal testing machine work for a tension test?
A universal testing machine, when used for a tension test, applies a load or force to the test specimen and measures the resulting elongation or deformation. As the load increases, the machine records the corresponding increase in length. From these data, a stress-strain curve can be plotted, providing valuable information about the material’s mechanical properties, such as tensile strength, yield strength, and modulus of elasticity.
What is tensile test equipment called?
Equipment used to perform a tensile test is typically referred to as a tensile testing machine or a universal testing machine. These machines come in a variety of configurations, but all are designed to apply a controlled tension load to a sample and measure the sample’s response.
Where would you use a tensile test?
Tensile tests are used across a wide range of sectors, including manufacturing, construction, automotive, aerospace, medical, and materials science. Anywhere that materials need to be selected, evaluated, or validated based on their mechanical properties, a tensile test is likely to be a fundamental part of the process.
Which is the most common type of tensile tester?
The most common type of tensile tester is the universal testing machine. Its popularity stems from its versatility—it is capable of performing tensile, compression, shear, flexural (bending), and cyclic tests, among others. It can be equipped with various fixtures and accessories to accommodate different materials and tests, making it a vital tool in many laboratories and testing facilities.
More informations
For more information about the Tensile Testing Machine, including price, commercial conditions, delivery times, and other details, please feel free to contact our team via email, phone, or WhatsApp
Contact us
Phones:
+1 (781) 328 – 2010
sales@biopdi.com
Address:
2 Burlington Woods Dr, Burlington, Massachusetts, United States
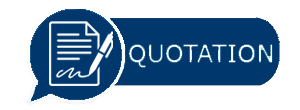
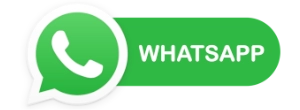