Comprehensive Guide to Axial Torsion Test: Definition, Applications & More
In this article, we’ll dive into the world of Axial Torsion Test. We will explore its principles, purpose, and different methods, along with the various materials it can test. This extensive guide will cover everything from machine components to standards and applications in the field of engineering and material science.
In the following text, you will find a summary of the topics that will be addressed in this article.
What is Axial Torsion Test?
The Axial-Torsion Test is a multi-faceted mechanical testing process that applies both axial (longitudinal) and torsional (twisting) forces to a sample. This examination allows for a complex understanding of how a material behaves under various simultaneous stress conditions.
The test involves:
- Axial Stress: This refers to the force applied along the longitudinal axis of the sample. It can be either tensile (pulling apart) or compressive (pushing together). Axial stress enables the analysis of properties like tensile strength, compressive strength, and elastic modulus.
- Torsional Stress: This is the twisting force applied to the sample, allowing the assessment of properties such as shear modulus and torsional strength. Torsional stress provides insights into how the material withstands twisting or rotational forces.
The Axial-Torsion Test, with its ability to apply and measure both axial and torsional forces, offers a comprehensive understanding of a material’s mechanical properties. It plays a crucial role in material science and engineering by simulating complex real-world conditions, guiding material selection, design, and quality assurance across various industries. Its application is not only confined to assessing the material’s fundamental properties but also serves as a powerful tool in advancing our understanding of how materials interact under multifaceted stress conditions.
Video about Axial Torsion Testing
Representation of Axial Torsion Testing
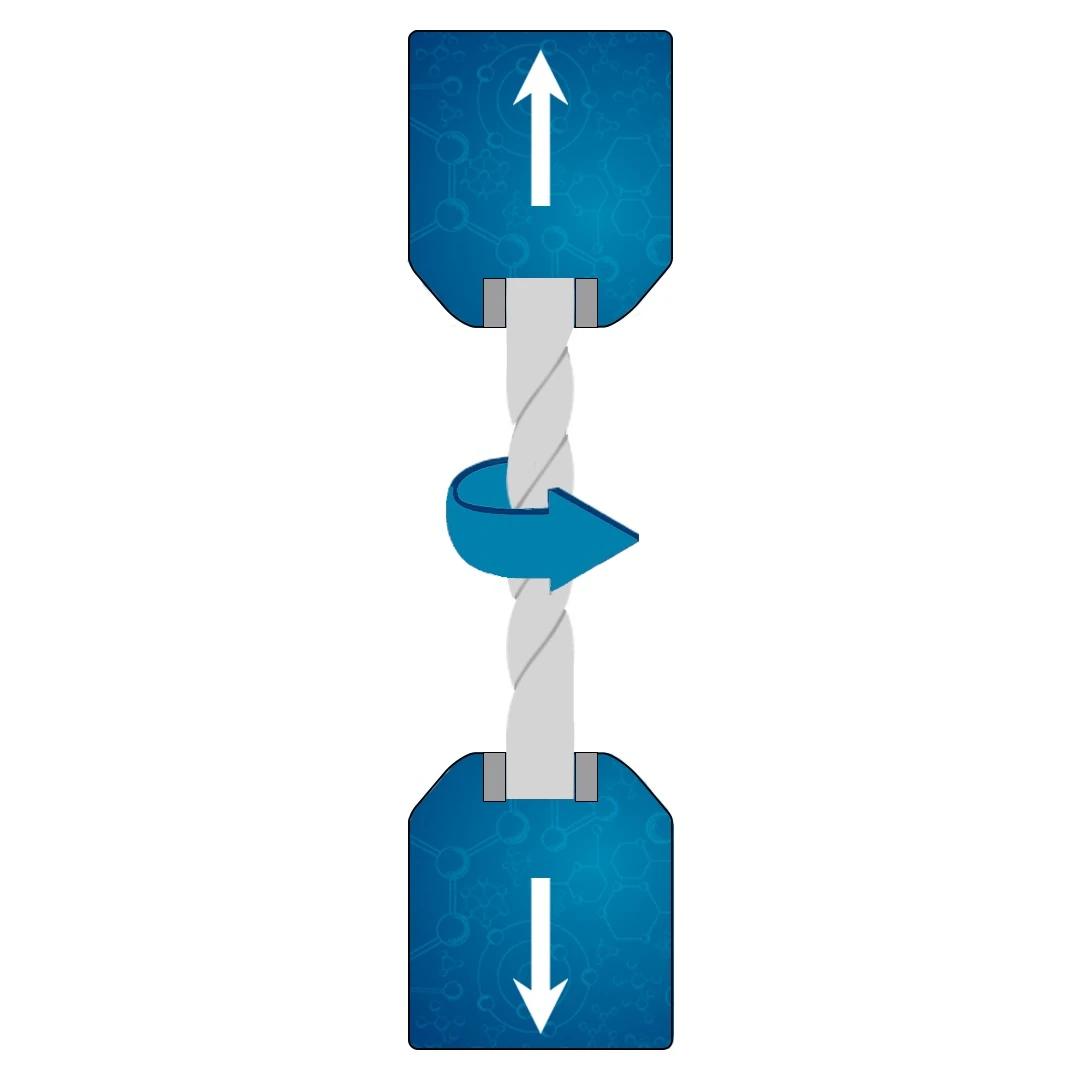
What Does Axial Torsion Test Measure?
The Axial-Torsion Test measures a material’s response to simultaneous axial (longitudinal) and torsional (rotational) stresses. Here’s a detailed look at what specifically this test measures:
Axial Properties:
- Tensile Strength: Measures the material’s ability to withstand pulling or stretching forces.
Compressive Strength: Assesses how the material responds to forces that compress or push it together. - Elastic Modulus: Determines the material’s elasticity or its ability to return to its original shape after being deformed.
Ductility: Evaluates how much a material can be deformed under tensile stress before breaking.
Torsional Properties:
- Torsional Strength: Measures the material’s ability to withstand twisting forces.
- Shear Modulus: Represents the material’s rigidity under shearing or twisting forces.
Torsional Fatigue Behavior: Assesses how the material behaves under repeated twisting loads, providing insights into its long-term durability.
Combined Stress Responses:
- Biaxial Fatigue Behavior: Analyzes how the material responds to repeated cycles of both axial and torsional loading, critical for predicting how it will behave in real-world conditions where these forces are often combined.
- Strain Response: Measures the deformation or strain in the material under combined loading, providing insights into how the material may behave when used in specific applications like automotive components or industrial machinery.
Fracture Characteristics:
- Fracture Toughness: Evaluates the material’s ability to resist crack propagation under combined stresses, a crucial factor in determining its long-term reliability.
Behavior Under Extreme Conditions:
- Creep Behavior: Measures how the material deforms slowly over time under constant stress, a factor that might be vital in high-temperature applications.
By examining these properties, the Axial-Torsion Test offers a comprehensive view of the material’s mechanical behavior. This understanding is vital in various applications such as design, quality control, failure analysis, and the selection of materials for specific functions within industrial, automotive, aerospace, and other engineering domains. The test’s ability to simulate real-world conditions makes it an indispensable tool in the field of material science and engineering.
What is the purpose of an Axial Torsion Test?
The purpose of an Axial-Torsion Test (biaxial test) is multifaceted, reflecting the complex nature of materials and the various stresses they encounter in real-world applications. Here are the primary objectives of conducting this test:
- Simulating Real-World Conditions: Materials in real-world applications often encounter combined stresses such as axial and torsional forces simultaneously. The Axial-Torsion Test is designed to simulate these conditions, providing a more accurate understanding of how the material will behave in actual use.
- Understanding Mechanical Properties: The test provides detailed insights into essential mechanical properties like tensile strength, compressive strength, torsional strength, ductility, and elastic modulus. It helps in characterizing the material’s resistance to deformation and failure under combined stresses.
- Material Selection and Design Guidance: By analyzing how materials react under combined loading, engineers and designers can make informed decisions about the selection of materials for specific applications. This information helps in optimizing designs for performance, durability, and safety.
- Assessment of Fatigue Behavior: The test offers vital information on how a material responds to repeated cycles of axial and torsional stresses, crucial in understanding its long-term durability and resistance to fatigue-related failure.
- Quality Control and Assurance: In industrial manufacturing, the Axial-Torsion Test is often used as a part of quality control protocols. It helps in ensuring that materials meet the required standards and specifications, ensuring consistency and reliability.
- Failure Analysis: By pushing materials to their limits, the Axial-Torsion Test can provide valuable insights into potential weaknesses or failure points. This information is vital for preventing material failures in critical applications such as aerospace, automotive, or medical devices.
- Research and Development: In material science and engineering, the Axial-Torsion Test is a valuable tool for research and development. It enables the study of new materials, coatings, or treatments, contributing to innovations in material technology.
- Compliance with Standards: By following specific ISO and ASTM standards, the Axial-Torsion Test helps manufacturers and researchers ensure that their materials comply with international regulations, enhancing credibility and acceptance in global markets.
- Evaluating Material Interactions: In some applications, understanding how different materials interact under combined stresses is vital. The Axial-Torsion Test provides insights into these interactions, aiding in the design of composite or multi-material components.
Types of Axial Torsion Test
The Axial Torsion Test can be classified into different types based on various parameters, including the method of applying forces, the material being tested, and the specific objectives of the test. Here are some primary types:
Based on Loading Method:
- Static Axial-Torsion Test: Involves applying constant axial and torsional loads to measure properties like strength, stiffness, and ductility.
- Dynamic Axial-Torsion Test: Assesses fatigue behavior by subjecting the material to repeated cycles of axial and torsional stresses.
Based on Temperature Conditions:
- Room Temperature Testing: Conducted under standard ambient conditions to evaluate material properties at room temperature.
- High-Temperature Testing: Assess how materials behave at elevated temperatures, vital for applications like aerospace and power generation.
Based on Material Type:
- Metallic Testing:Focuses on metals and alloys, measuring properties like tensile strength, compressive strength, and torsional strength.
- Polymeric Testing:Evaluates polymers, considering aspects like elasticity, plasticity, and viscoelastic behavior.
- Ceramic Testing:Assesses brittle materials like ceramics for their resistance to cracking and deformation.
- Composite Testing:Studies complex materials made from different constituents, evaluating their combined mechanical behavior.
Based on Test Configuration:
- Uniaxial Torsion with Axial Loading: Applies torsional loading along with a controlled axial load, assessing the material’s combined response.
- Multiaxial Loading: More complex configurations involving multiple axes of loading, allowing a comprehensive understanding of material behavior.
Parts and Components of an Axial Torsion Test Machine
An Axial Torsion Test Machine, often referred to as a biaxial machine, is a complex instrument designed to apply both axial and torsional loads to a specimen. Here are the primary parts and components of such a machine:
Load Frame:
- Columns: Provide structural support to the entire setup.
- Crosshead: A movable part that can be adjusted to accommodate various specimen lengths.
Loading System:
- Axial Actuator: Applies a vertical load for tension or compression testing.
- Torsional Actuator: Delivers a twisting motion to apply torsional loads.
- Hydraulic or Electromechanical Drive: Powers the actuators.
Grips and Fixtures:
- Axial Grips: Hold the specimen securely in place for tensile or compressive loading.
- Torsional Fixtures: Adapted to apply a twisting force without slippage.
Sensors and Transducers:
- Load Cells: Measure the force applied to the specimen.
- Torque Sensors: Measure the torsional load.
- Extensometers: Measure changes in length (axial strain).
- Rotary Encoders: Detect angular displacement (torsional strain).
- Temperature Sensors: If temperature control is needed, these sensors monitor the specimen’s temperature.
Control System:
- Controller: Governs the actuators’ movement, following the prescribed load pattern.
- User Interface: Enables the operator to set up and monitor the test, including load levels, rates, and cycles.
Data Acquisition System:
- Analog-to-Digital Converters: Translate the analog signals from sensors into digital data.
- Software: Collects, analyzes, and stores the data, often providing real-time visualization and post-test analysis.
Safety Features:
- Emergency Stop Buttons: Allow quick termination of the test if problems are detected.
- Protective Shields: Protect operators from debris in case of specimen failure.
Environmental Chamber (optional):
- Allows testing under controlled temperature and humidity conditions.
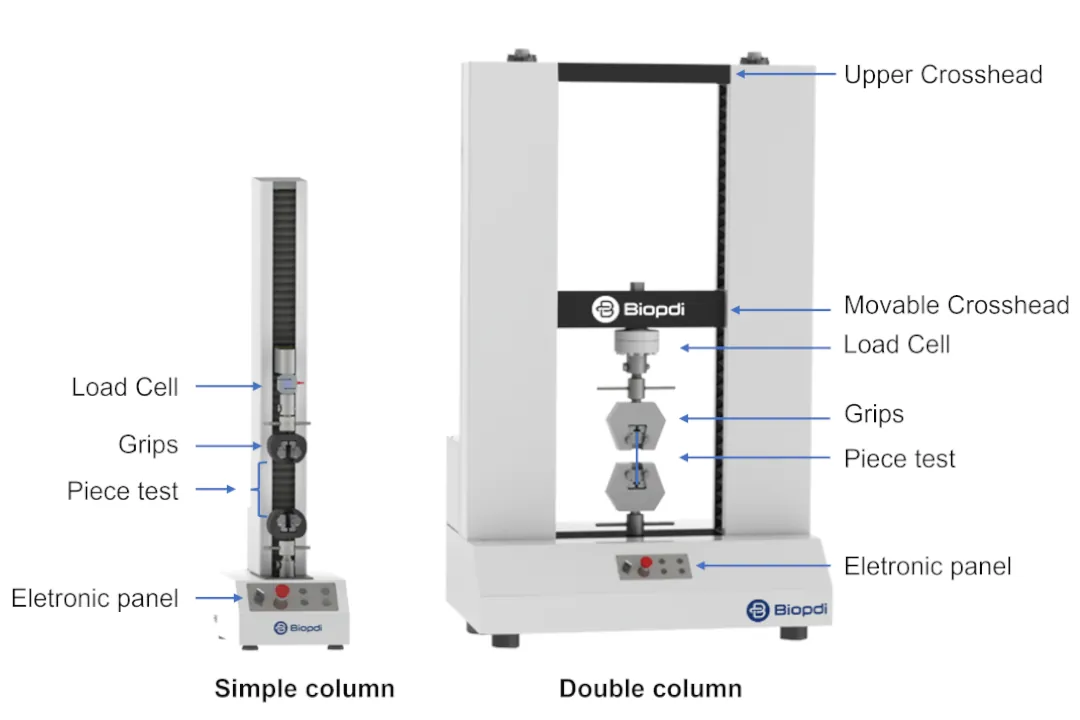
Conducting an Axial Torsion Test using an Axial Torsion Test Machine
Conducting an Axial-Torsion Test requires a systematic approach to ensure that the results are accurate and meaningful. Here are the typical procedures for performing this test using an Axial-Torsion Test Machine:
Preparation:
- Understand Test Requirements: Define the parameters such as load, strain rate, and test type (tension, compression, torsion, etc.).
- Select and Prepare the Specimen: Cut and shape the specimen according to standard dimensions and ensure it’s free of defects.
Machine Setup:
- Install Grips and Fixtures: Use appropriate axial and torsional grips that match the specimen geometry.
- Calibrate Sensors: Ensure that the load cells, extensometers, and other sensors are properly calibrated.
- Set Up Environmental Chamber (if required): Pre-set temperature or humidity conditions.
Specimen Mounting:
- Place the Specimen: Carefully align the specimen within the grips to prevent any bending or misalignment.
- Attach Extensometers: If required, for precise strain measurement.
Test Configuration:
- Input Test Parameters: Configure the axial and torsional loads, strain rates, cycles, and other required settings in the control software.
- Safety Checks: Ensure all safety barriers are in place, and the emergency stop function is accessible.
Performing the Test:
- Start the Test: Begin the automated testing procedure via the control system.
- Monitor the Test: Keep an eye on real-time data and visual indications of the specimen’s behavior.
- Emergency Stop if Necessary: Terminate the test if any unexpected behavior is observed.
Data Collection and Analysis:
- Record Data: The system will continuously log essential data such as load, displacement, torque, etc.
- Analyze Results: Post-test analysis to derive properties like stress-strain curves, modulus, strength, and more.
Post-Test Activities:
- Remove Specimen: Carefully disengage and preserve the specimen if further examination is needed.
- Clean and Reset the Machine: Prepare the machine for the next test or maintenance.
- Report Generation: Compile the test results into a comprehensive report, including details of the procedure, observations, and conclusions.
Data obtained from a Axial torsion test
The Axial-Torsion Test (biaxial test) using an Axial-Torsion Test Machine provides a comprehensive set of data that can be analyzed to understand material behavior under combined axial and torsional loading. Here’s a list of the common data obtained during this test:
Axial Data:
- Axial Load: The force applied along the length of the specimen.
- Axial Displacement: The change in length of the specimen.
- Axial Stress: The force per unit area in the axial direction.
- Axial Strain: The change in length divided by the original length.
Torsional Data:
- Torque: The twisting force applied to the specimen.
- Angular Displacement: The angle through which the specimen has been twisted.
- Shear Stress: The force per unit area in the torsional direction.
- Shear Strain: The change in angle divided by the original length.
Stress-Strain Curves:
- Axial Stress-Strain Curve: Relationship between axial stress and strain.
- Shear Stress-Strain Curve: Relationship between shear stress and shear strain.
Material Properties:
- Modulus of Elasticity: Stiffness in the axial direction.
- Shear Modulus: Stiffness in the torsional direction.
- Yield Strength: Stress at which permanent deformation begins.
- Ultimate Strength: Maximum stress that can be sustained.
Cyclic and Fatigue Data (if applicable):
- Number of Cycles: For fatigue testing.
- Amplitude and Frequency: Description of loading cycles.
- Fatigue Life: Number of cycles until failure.
Failure Information:
- Failure Mode: Description of how the specimen failed (e.g., fracture, buckling).
- Location of Failure: Specific location where failure initiated.
The main standards for obtaining the Axial Torsion Test
Axial-Torsion Tests are governed by specific standards that provide guidelines on how the test should be conducted, ensuring accuracy, repeatability, and comparability of the results. Here are some standards:
ISO Standards:
- ISO 80369-1: Specifies general requirements for small-bore connectors, which may be used in Axial-Torsion Tests of medical devices and components.
- ISO 594-1: This standard was related to the conical fittings with a 6% (Luer) taper for syringes, needles, and certain other medical equipment. It could be relevant for testing the axial-torsional properties of these connections but has been replaced by ISO 80369 series.
- ISO 594-2: Similar to ISO 594-1, this part deals with testing of Luer lock fittings and has also been replaced by the ISO 80369 series.
ASTM Standards:
- ASTM F543: Standard Specification and Test Methods for Metallic Medical Bone Screws (may include axial-torsion testing for evaluating screw performance).
- ASTM F2077: Test Methods for Intervertebral Body Fusion Devices (can include axial-torsion testing as part of the evaluation process).
- ASTM F1717: Standard Test Methods for Spinal Implant Constructs in a Vertebrectomy Model (may involve axial-torsion testing to simulate physiological conditions).
- ASTM E2207: Standard Practice for Strain-Controlled Axial-Torsion Fatigue Testing with Thin-Walled Tubular Specimens.
Conclusion
The Axial-Torsion Test (biaxial test) stands as a vital procedure in material science and engineering, encompassing a broad spectrum of materials like metals, polymers, ceramics, and composites.
By simultaneously applying axial and torsional loads, it offers insights into complex material behaviors. Governed by specific ISO and ASTM standards, the test ensures consistent and reliable data across various industries. From aerospace to healthcare, its applications are extensive, enabling innovation and quality assurance.
In essence, the Axial-Torsion Test represents a cornerstone in advancing technological growth, bridging theoretical understanding with real-world application.
FAQs
What is an Axial-Torsion Test (biaxial test)?
The Axial-Torsion Test is a laboratory procedure used to simultaneously apply axial (tensile/compressive) and torsional (twisting) loads on a material specimen. It’s used to understand how the material behaves under complex loading conditions.
What is the purpose of an Axial-Torsion Test?
The test is essential for characterizing material properties, such as stiffness, yield strength, and fatigue behavior. It provides valuable insights into the material’s performance under real-world conditions.
What types of materials can be tested with an Axial-Torsion Test?
Various materials like metals, polymers, ceramics, and composites can be evaluated using this test. It’s widely applicable across industries and research fields.
How is an Axial-Torsion Test conducted?
The test is conducted using specialized machinery, which applies controlled axial and torsional forces. The material’s response is recorded and analyzed to understand its mechanical properties.
What are the main standards for an Axial-Torsion Test?
The test is conducted according to specific international standards, including ISO 80369-1, ISO 594-1, ISO 594-2, ASTM F543, ASTM F2077, ASTM F1717, and ASTM E2207, among others.
What data is obtained from an Axial-Torsion Test?
The test provides critical information about stress-strain relationships, shear modulus, elastic limits, and potential failure modes. These data are vital for design, manufacturing, and quality control purposes.
How are samples prepared for the test?
Sample preparation involves careful selection and machining to specific dimensions, ensuring that the specimen represents the material accurately. Adherence to standards is essential for consistency.
Where are Axial-Torsion Tests applied?
The test has wide-ranging applications, from material characterization in aerospace and automotive to medical implants, construction, energy sector, manufacturing processes, and research and development.
What machinery is used in Axial-Torsion Testing?
A specialized Axial-Torsion Test Machine, equipped with the necessary components to apply and measure both axial and torsional loads, is used to conduct the test.
Why are Axial-Torsion Tests important in engineering and material science?
These tests bridge the gap between theoretical models and real-world applications, allowing for the design and development of materials that meet specific demands and performance criteria. They play a crucial role in innovation and quality assurance across various industries.
See more relevant posts
TENSILE TEST
Tensile testing is a crucial mechanical test used to evaluate the strength and ductility of materials. It involves applying a controlled force. See more
COMPRESSION TEST
Compression testing is a fundamental evaluation method employed to assess a material's ability to withstand compressive forces. See more
SHEAR TEST
Shear testing examines a material's response to forces acting parallel to its surface. By applying a force that causes one part of the material. See more
BEND TEST
Bend testing is a mechanical test that determines a material's flexibility and resistance to fracture under bending forces. See more
FLEXURAL TEST
Flexural testing, also known as the three-point bend test, is employed to measure a material's resistance to bending or flexural stress. See more
FRICTION TEST
Coefficient of friction test measures the amount of resistance between two surfaces in contact when one moves relative to the other. See more
TEAR TEST
Tear test determines a material's resistance to tearing forces, often encountered in applications involving thin films, fabrics. See more
PEEL TEST
Peel testing evaluates the strength of adhesion between two materials, typically an adhesive and a substrate. The test involves separating. See more
BOND TEST
Bond test measures the strength of a bond between two materials. It's used in adhesive and weld test. It helps in determining the reliability of joints and interfaces. See more
INDENTATION TEST
Indentation Force Deflection (IFD) is used to characterize the cushioning or compressive properties of a material, especially foams and soft polymers. See more
FRACTURE TEST
Fracture toughness is a material's ability to resist crack propagation. This property is vital for assessing a material's suitability for applications where structural. See more
PUNCTURE TEST
Puncture test examines a material's ability to withstand penetration by sharp objects or forces. This test to evaluate puncture strength and design materials. See more
CRUSH TEST
Crush resistance test measures a material's ability to resist deformation, particularly in terms of compressive force. See more
TORSION TEST
Torsion testing is a critical method in materials engineering, examining how products and materials behave under twisting forces. See more
AXIAL TORSION TEST
Axial torsion test examines a material's behavior when subjected to simultaneous axial and torsional loads. This test to study shear stress. See more
FATIGUE TEST
Fatigue Testing is the evaluation of a material's endurance and failure under repeated stress and cyclic loading conditions. See more.
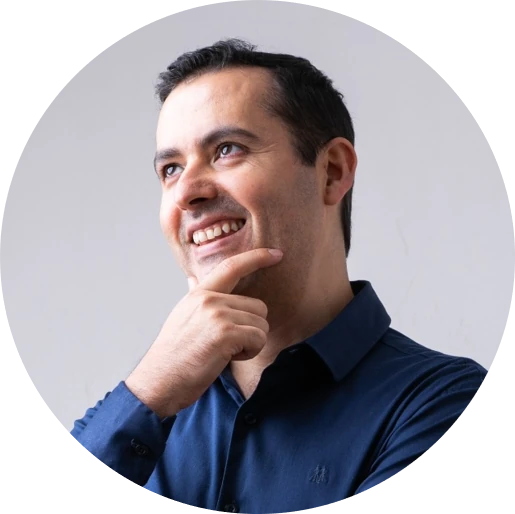
Author: Mardoqueu M. Costa (Entrepreneur, researcher and writer). I have been working for several years in materials science and engineering and biomedical engineering with emphasis on Entrepreneurship. My focus is on the development of equipment, software, mechanical tests, and the evaluation and creation of new businesses. As a researcher and writer, I have contributed to scientific publications and patents, also working as a technical-scientific consultant for several companies. This integrated approach reflects my commitment to innovation and impact in the technology industry.
Contact us
Phones:
+1 (781) 328 - 2010
sales@biopdi.com
Address:
2 Burlington Woods Dr, Burlington, Massachusetts, United States
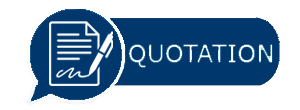
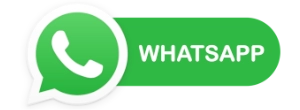