Fracture Toughness Testing: A Detailed Approach to Methods and Applications
In this article, we will delve into the concept of fracture toughness testing, an essential aspect in materials science that defines a material’s ability to resist crack propagation. We will explore its definition, testing methods, relevance, applications, standards, and much more to provide a comprehensive understanding of this vital subject.
What is the Fracture toughness?
Fracture toughness is a quantitative measure of a material’s ability to resist the propagation of a crack. It defines how well a material can withstand the growth of existing cracks under applied stress and is typically measured in units of MPa√m (Mega Pascals times the square root of meters).
In essence, fracture toughness gives us an understanding of how much energy a material can absorb before it begins to crack and ultimately fail. This property is crucial in the design of components that are subject to challenging mechanical loads and must maintain structural integrity, such as in aerospace, automotive, and civil engineering applications.
What is the Fracture toughness testing?
Fracture toughness testing is the process of determining a material’s ability to resist the growth and propagation of an existing crack under applied stress.
This testing method quantifies the material’s fracture toughness, which is a critical property that indicates how much stress intensity a material can endure at the tip of a crack before it starts to grow.
The testing involves preparing a specimen with a pre-existing crack, applying a controlled load, monitoring the crack’s behavior, and calculating the fracture toughness value. It plays a vital role in evaluating materials for applications where structural integrity and resistance to crack growth are paramount
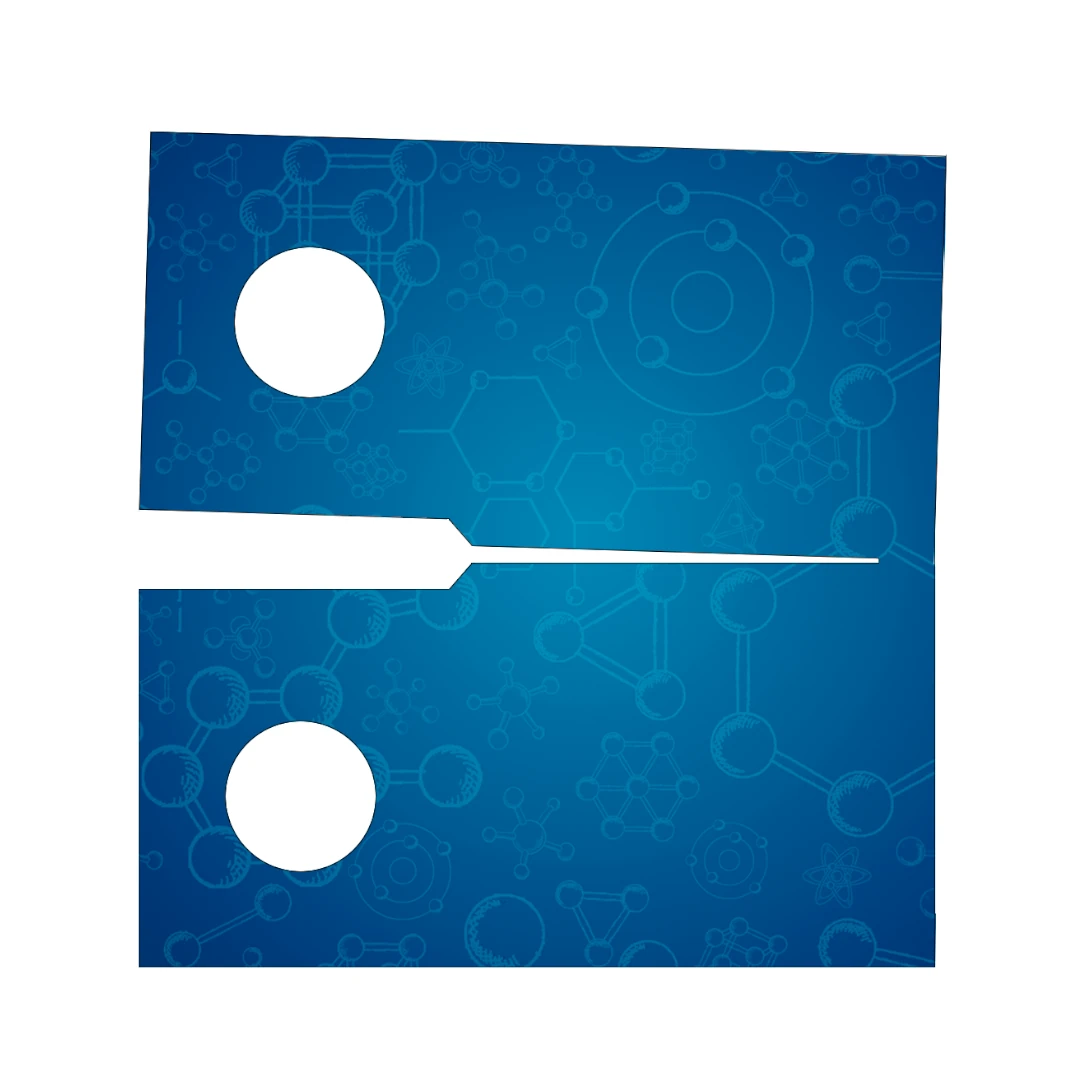
What is the Fracture Toughness Formula?
The formula for calculating fracture toughness (K_IC) is often given as:
where P is the load, B is the thickness of the specimen, W is the width, a is the crack length, and f(a/W) is a geometric function depending on the specimen’s shape.
Importance of Fracture Toughness Test
Understanding fracture toughness is vital for the design and engineering of materials used in applications where structural integrity and safety are paramount. It helps to predict the material’s behavior under stress and to choose the right material for specific applications.
Advantages of Using the Fracture Toughness Test
- Accurate Prediction: Helps in predicting how materials will behave under real-world conditions.
- Material Selection: Assists engineers in selecting the most appropriate materials for specific applications.
- Safety Concerns: Provides data that can prevent catastrophic failures in structural applications.
Types of Fracture Toughness Test
- Linear Elastic Fracture Toughness (LEFM): Used for brittle materials.
- Elastic-Plastic Fracture Toughness (EPFM): For materials that show some plastic deformation before fracturing.
- J Integral Method: Useful for materials that exhibit both elastic and plastic deformation.
Properties Obtained in the Fracture Toughness Test
- Crack Resistance Curve
- Stress-Intensity Factor
- Critical Stress-Intensity Factor
- Elastic-Plastic Transition Behavior
How to Calculate the Fracture Toughness Test?
Calculating fracture toughness involves measuring the load and displacement during the test, using the previously mentioned formula, and considering the geometry of the specimen.
Materials Tested with Fracture Toughness Test
Metallic:
- Steel: High fracture toughness, typically around 50-200 MPa√m.
- Aluminum: Lower than steel, around 20-50 MPa√m.
Polymers:
- Polycarbonate: Moderate toughness, 1-5 MPa√m.
- Polyethylene: Highly variable, 0.1-10 MPa√m.
Ceramics:
- Alumina: Quite brittle, 3-4 MPa√m.
- Silicon Carbide: Around 3-5 MPa√m.
Composites:
- Carbon Fiber Reinforced Plastics (CFRP): 5-25 MPa√m.
- Glass Fiber Reinforced Plastics (GFRP): 2-20 MPa√m.
Universal testing machine used for Fracture Toughness Testing
A Universal Testing Machine (UTM), also known as a universal tester, materials testing machine, or tensile testing machine, is a crucial piece of equipment in the field of material science and engineering. It’s versatile enough to perform various types of mechanical tests, including fracture toughness testing.
Below are the essential parts and components of a UTM used in fracture toughness testing:
- Load Frame: The load frame is the primary structure of the UTM, typically composed of two strong vertical columns connected by a top and bottom crosshead. This rigid structure is designed to accommodate the high stress generated during testing.
- Crossheads: These are positioned at the top and bottom of the load frame. The upper crosshead is usually stationary, while the lower crosshead can be adjusted depending on the length of the specimen.
- Load Cell: This is a transducer that converts force into an electrical signal, allowing the UTM to measure the load applied to the specimen. Its accurate calibration is crucial for precise testing.
- Actuator: Typically driven by hydraulic, mechanical, or electromechanical means, the actuator applies the required load on the specimen. In some machines, the actuator’s position is adjustable to accommodate specimens of different sizes.
- Grips/ Fixtures: These hold the test specimen in place during testing. For fracture toughness testing, a specific shear test fixture might be used. The grips/fixtures must be chosen carefully to ensure they don’t slip or induce additional stresses that could interfere with the test results.
- Extensometer: This device is used to measure the deformation or strain in the test specimen during the application of force.
- Control Unit: This component controls the speed and direction of the load, the parameters of the test, and other variables. In modern UTMs, the control unit is typically a computer running specialized software.
- Output Device: This could be a computer monitor or a printer that provides a visual representation of the test results, often in the form of a stress-strain graph or a detailed test report.
- Safety Guards: These are essential to protect operators from flying debris in case of a specimen fracture or fixture failure.
Each of these components plays a critical role in the functioning of a UTM. For accurate and reliable results, the UTM should be regularly calibrated and maintained according to the manufacturer’s guidelines and relevant industry standards.
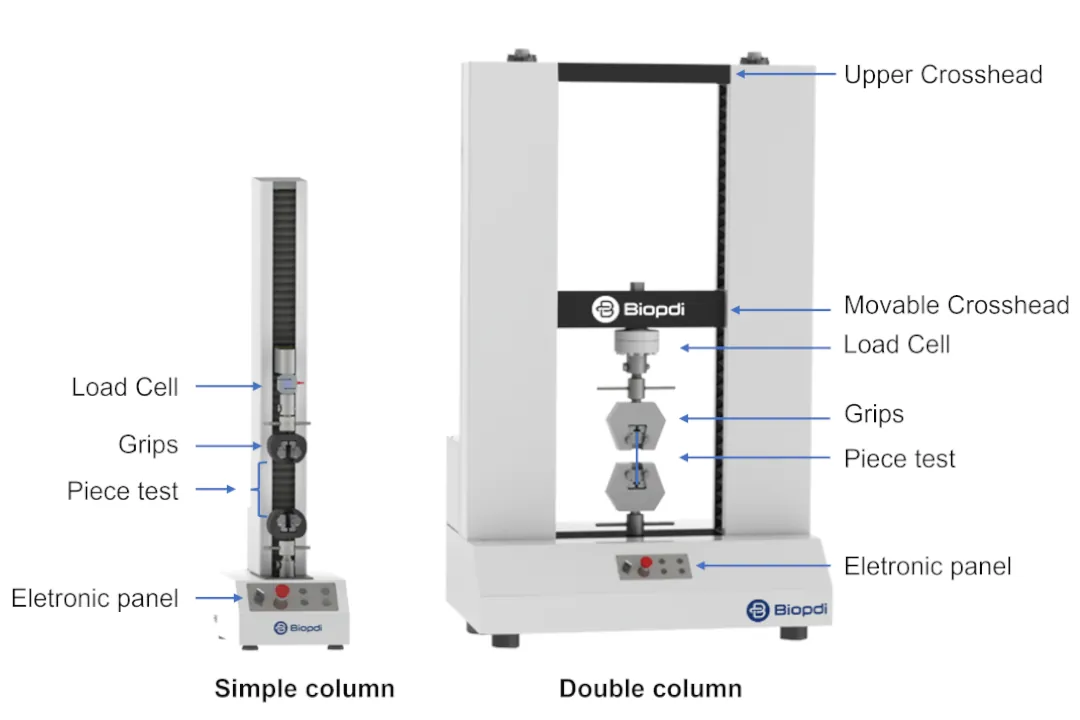
Universal Testing Machine used in the shear test
Procedures for Conducting a Fracture Toughness Test using a Universal Testing Machine
- Prepare the specimen with a pre-crack.
- Mount the specimen in the testing machine.
- Apply the load gradually.
- Record the load and displacement data.
- Analyze the data to calculate fracture toughness.
Data Obtained in the Fracture Toughness Test Using the Universal Testing Machine
- Load vs. Displacement Curve
- Crack Length
- Fracture Toughness Value
Samples/Specimens Used
Typically, specimens are carefully prepared with a pre-existing crack and must meet specific geometric requirements. They are often rectangular or disc-shaped.
Standards for Obtaining the Fracture Toughness Testing
The main standards used in the field of materials science for obtaining fracture toughness, split between ISO and ASTM standards:
ISO Standards:
- ISO 12135: This standard outlines the procedure for fracture toughness testing in metallic materials using a method that involves pre-cracked specimens.
- ISO 13586: It specifies a method for determining the plane-strain (linear elastic) fracture toughness of metallic materials.
- ISO 1820: This standard relates to the determination of fracture toughness of monolithic ceramics at room temperature.
- ISO 23146: Specifies the method for determining plane-strain fracture toughness of high-strength hydraulic cement mortars.
- ISO 10113: Though primarily focused on metallic materials, this standard also has relevance in the context of fracture toughness for specific applications.
ASTM Standards:
- ASTM E399: This standard test method is used to determine the plane-strain fracture toughness of metallic materials.
- ASTM E1820: This specification covers the determination of fracture toughness using procedures and specimen configurations, including those for elastic-plastic fracture.
- ASTM E1290: Describes the determination of fracture toughness using crack-tip opening displacement (CTOD) in metallic materials.
- ASTM E647: This standard provides a test method for measuring the growth of fatigue cracks in metallic materials, relevant for understanding fracture toughness.
- ASTM D5045: This standard focuses on plane-strain fracture toughness and strain energy release rates for plastic materials.
These standards provide the guidelines and procedures that ensure the reliability, consistency, and repeatability of fracture toughness testing across different materials and industries. They take into account various factors such as specimen geometry, loading conditions, and environmental factors to ensure that the test results are accurate and meaningful.
FAQs
What is the test for fracture toughness?
The test for fracture toughness involves preparing a specimen with a pre-existing crack and subjecting it to controlled loading conditions to determine the material’s ability to resist crack growth. It’s often performed using a Universal Testing Machine.
What is the ASTM standard for fracture toughness?
ASTM E399 is a widely used standard for determining the plane-strain fracture toughness of metallic materials. Other ASTM standards like ASTM E1820 and ASTM E647 also deal with aspects of fracture toughness.
Which test is used to measure fracture toughness of materials?
Fracture toughness is measured using a specific test that typically involves a pre-cracked specimen and controlled loading conditions. Standards like ASTM E399 and ISO 12135 provide guidelines for conducting these tests.
What test is used to measure toughness?
Toughness, including both fracture toughness and impact toughness, can be measured using various tests, including Charpy or Izod impact tests, and tests defined by standards like ASTM E399 for fracture toughness.
What is the ASTM standard toughness test?
ASTM standards for toughness tests include ASTM E399 for plane-strain fracture toughness and ASTM E23 for Charpy impact testing, among others.
What is a good fracture toughness value?
A “good” fracture toughness value is relative and depends on the specific application and material. Higher values generally indicate better resistance to crack propagation, but the required value will depend on the specific demands of the intended use.
What are the types of toughness test?
Toughness tests can include fracture toughness tests (guided by standards like ASTM E399), impact toughness tests (such as Charpy or Izod tests), and various other tests depending on the material and application.
What is the difference between hardness test and toughness test?
Hardness tests measure a material’s resistance to deformation or scratching, while toughness tests assess the material’s ability to absorb energy before fracturing. Essentially, hardness is related to surface resistance, while toughness is about a material’s resistance to breaking or cracking.
How is toughness determined?
Toughness is determined through specific testing procedures that measure a material’s ability to absorb energy before fracturing. This may include fracture toughness tests that follow standards like ASTM E399 or impact tests like the Charpy test, depending on the particular aspect of toughness being evaluated.
See more relevant posts
TENSILE TEST
Tensile testing is a crucial mechanical test used to evaluate the strength and ductility of materials. It involves applying a controlled force. See more
COMPRESSION TEST
Compression testing is a fundamental evaluation method employed to assess a material's ability to withstand compressive forces. See more
SHEAR TEST
Shear testing examines a material's response to forces acting parallel to its surface. By applying a force that causes one part of the material. See more
BEND TEST
Bend testing is a mechanical test that determines a material's flexibility and resistance to fracture under bending forces. See more
FLEXURAL TEST
Flexural testing, also known as the three-point bend test, is employed to measure a material's resistance to bending or flexural stress. See more
FRICTION TEST
Coefficient of friction test measures the amount of resistance between two surfaces in contact when one moves relative to the other. See more
TEAR TEST
Tear test determines a material's resistance to tearing forces, often encountered in applications involving thin films, fabrics. See more
PEEL TEST
Peel testing evaluates the strength of adhesion between two materials, typically an adhesive and a substrate. The test involves separating. See more
BOND TEST
Bond test measures the strength of a bond between two materials. It's used in adhesive and weld test. It helps in determining the reliability of joints and interfaces. See more
INDENTATION TEST
Indentation Force Deflection (IFD) is used to characterize the cushioning or compressive properties of a material, especially foams and soft polymers. See more
FRACTURE TEST
Fracture toughness is a material's ability to resist crack propagation. This property is vital for assessing a material's suitability for applications where structural. See more
PUNCTURE TEST
Puncture test examines a material's ability to withstand penetration by sharp objects or forces. This test to evaluate puncture strength and design materials. See more
CRUSH TEST
Crush resistance test measures a material's ability to resist deformation, particularly in terms of compressive force. See more
TORSION TEST
Torsion testing is a critical method in materials engineering, examining how products and materials behave under twisting forces. See more
AXIAL TORSION TEST
Axial torsion test examines a material's behavior when subjected to simultaneous axial and torsional loads. This test to study shear stress. See more
FATIGUE TEST
Fatigue Testing is the evaluation of a material's endurance and failure under repeated stress and cyclic loading conditions. See more.
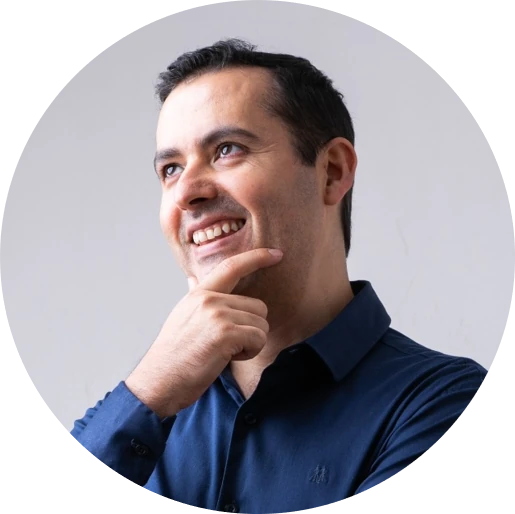
Author: Mardoqueu M. Costa (Entrepreneur, researcher and writer). I have been working for several years in materials science and engineering and biomedical engineering with emphasis on Entrepreneurship. My focus is on the development of equipment, software, mechanical tests, and the evaluation and creation of new businesses. As a researcher and writer, I have contributed to scientific publications and patents, also working as a technical-scientific consultant for several companies. This integrated approach reflects my commitment to innovation and impact in the technology industry.
Contact us
Phones:
+1 (781) 328 - 2010
sales@biopdi.com
Address:
2 Burlington Woods Dr, Burlington, Massachusetts, United States
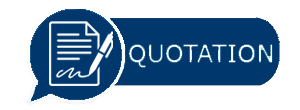
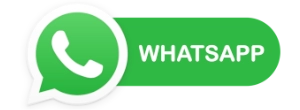